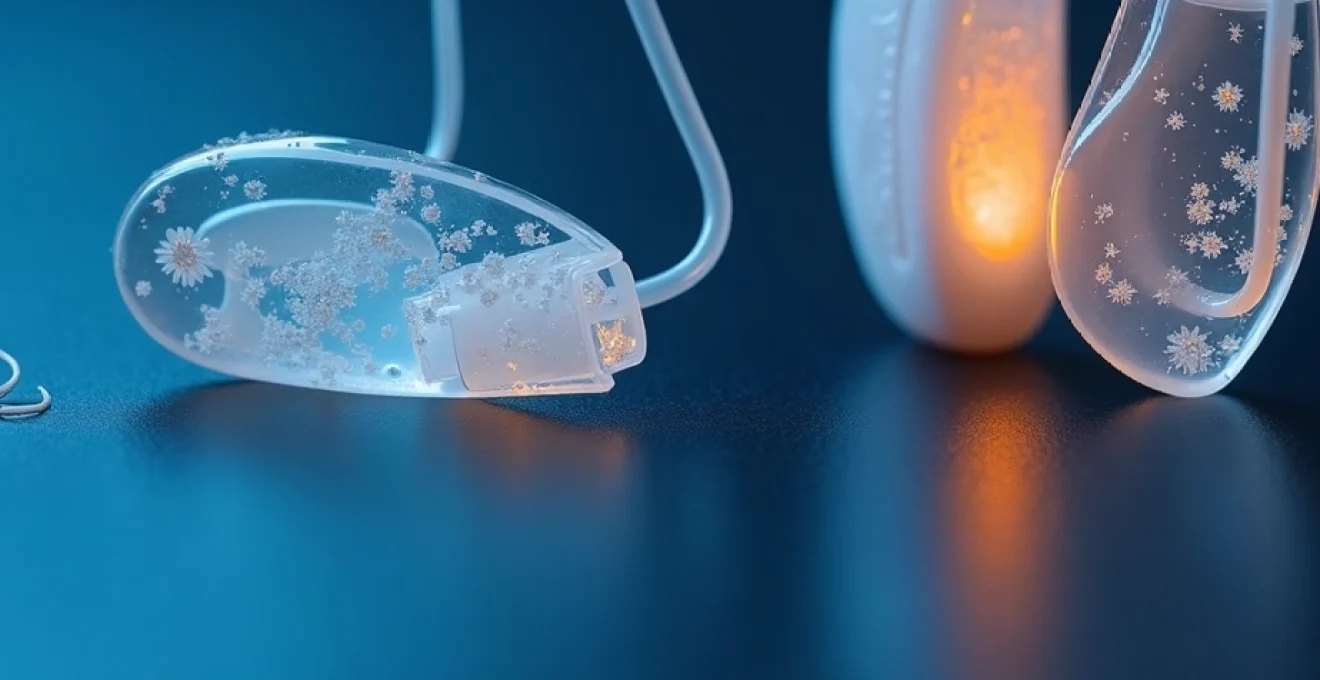
L'impression 3D révolutionne la conception et la fabrication de prothèses auditives sur mesure. Cette technologie de pointe permet de créer des appareils parfaitement adaptés à la morphologie unique de chaque patient, offrant un confort et des performances acoustiques inégalés. En combinant numérisation 3D, modélisation assistée par ordinateur et fabrication additive, les audioprothésistes peuvent désormais proposer des solutions auditives hautement personnalisées et esthétiques. Explorons les innovations qui transforment ce domaine médical grâce à l'impression 3D.
Technologie d'impression 3D pour prothèses auditives
L'impression 3D, également appelée fabrication additive, permet de créer des objets tridimensionnels en déposant des matériaux couche par couche. Pour les prothèses auditives, on utilise principalement deux technologies : la stéréolithographie (SLA) et le frittage sélectif par laser (SLS). Ces procédés offrent une précision et une qualité de surface exceptionnelles, essentielles pour des appareils en contact direct avec le conduit auditif.
La SLA utilise un laser pour polymériser une résine liquide photosensible, tandis que le SLS fusionne des poudres thermoplastiques à l'aide d'un laser puissant. Ces deux technologies permettent d'obtenir des pièces aux géométries complexes avec une précision de l'ordre de quelques microns. Les imprimantes 3D dédiées à l'audioprothèse intègrent souvent des fonctionnalités spécifiques comme la calibration automatique ou le contrôle de la température pour garantir une qualité constante.
L'un des principaux avantages de l'impression 3D est la possibilité de produire des séries unitaires de façon économique. Chaque prothèse peut être conçue sur mesure sans surcoût significatif, contrairement aux méthodes de fabrication traditionnelles. Cette flexibilité ouvre la voie à une personnalisation poussée des appareils auditifs.
Matériaux biocompatibles pour prothèses auditives imprimées
Le choix des matériaux est crucial pour garantir le confort, la durabilité et la sécurité des prothèses auditives imprimées en 3D. Les fabricants ont développé des résines et des poudres spécifiquement formulées pour répondre aux exigences de biocompatibilité et de performances acoustiques.
Résines photopolymérisables médicales
Les résines utilisées en SLA font l'objet d'une attention particulière. Elles doivent être biocompatibles, hypoallergéniques et résistantes dans le temps. Des formulations spéciales intègrent des propriétés antibactériennes pour limiter les risques d'infection. Certaines résines permettent même d'obtenir différentes duretés au sein d'une même pièce, offrant par exemple un canal auditif souple pour plus de confort.
Le polyéthylène glycol diacrylate
(PEGDA) est un exemple de résine largement utilisée pour sa biocompatibilité et ses propriétés mécaniques adaptées. D'autres résines comme le méthacrylate de méthyle
offrent une excellente transparence, appréciée pour les coques d'appareils intra-auriculaires discrets.
Filaments thermoplastiques certifiés
Pour l'impression FDM (dépôt de fil fondu), des filaments thermoplastiques biocompatibles ont été développés. Le polylactide (PLA) médical et certains polyamides offrent un bon compromis entre facilité d'impression et propriétés mécaniques. Ces matériaux sont souvent utilisés pour les prototypes ou les coques externes des appareils.
Nanocomposites acoustiques avancés
La recherche s'oriente vers des matériaux nanocomposites combinant polymères et nanoparticules pour améliorer les propriétés acoustiques. Ces matériaux "intelligents" peuvent par exemple absorber certaines fréquences sonores indésirables tout en amplifiant d'autres. L'impression 3D permet de contrôler précisément la répartition de ces nanoparticules au sein de la structure de la prothèse.
Caractérisation des propriétés mécaniques
Les propriétés mécaniques des matériaux imprimés en 3D peuvent différer de celles des matériaux moulés traditionnels. Une caractérisation précise est nécessaire pour garantir la durabilité et les performances acoustiques des prothèses. Des tests de résistance à la flexion, à l'abrasion et au vieillissement sont systématiquement réalisés.
La biocompatibilité et les performances à long terme des matériaux d'impression 3D font l'objet d'une surveillance constante. Les fabricants doivent se conformer à des normes strictes comme l'ISO 10993 pour garantir la sécurité des patients.
Conception numérique et modélisation 3D
La conception de prothèses auditives imprimées en 3D repose sur des outils numériques avancés permettant de créer des modèles parfaitement adaptés à l'anatomie de chaque patient. Cette approche sur mesure améliore considérablement le confort et les performances acoustiques des appareils.
Scanners 3D intra-auriculaires
La première étape consiste à numériser avec précision la forme du conduit auditif et de l'oreille externe du patient. Des scanners 3D intra-auriculaires miniaturisés permettent de capturer la géométrie complexe de l'oreille en quelques secondes. Ces appareils utilisent généralement la technologie de lumière structurée ou la photogrammétrie pour créer un modèle 3D détaillé.
Les scanners les plus avancés intègrent des fonctionnalités comme la détection automatique des points de référence anatomiques ou la compensation des mouvements du patient. Certains modèles permettent même de réaliser un scan dynamique pour observer les déformations du conduit auditif lors de la mastication ou de la parole.
Logiciels CAO spécialisés pour l'audioprothèse
Une fois le scan 3D obtenu, des logiciels de conception assistée par ordinateur (CAO) spécialisés sont utilisés pour modéliser la prothèse. Ces outils intègrent des fonctionnalités spécifiques à l'audioprothèse comme la création automatique de canaux acoustiques ou l'optimisation de l'emplacement des composants électroniques.
Les logiciels CAO pour l'audiologie permettent également de simuler le comportement acoustique de la prothèse et d'ajuster sa forme pour obtenir les meilleures performances. Des bibliothèques de composants standardisés (écouteurs, microphones, etc.) facilitent l'intégration des éléments électroniques dans le design.
Optimisation topologique pour l'acoustique
L'optimisation topologique est une technique de conception générative qui permet de créer des structures complexes optimisées pour des contraintes spécifiques. Dans le cas des prothèses auditives, cette approche est utilisée pour optimiser la propagation du son et minimiser les résonances indésirables.
Des algorithmes d'optimisation topologique spécialisés peuvent par exemple créer des structures internes complexes qui améliorent la directivité des microphones ou réduisent les distorsions acoustiques. Ces géométries optimisées, souvent impossibles à fabriquer avec des méthodes traditionnelles, sont parfaitement adaptées à l'impression 3D.
Simulation numérique des performances auditives
Avant la fabrication, des simulations numériques poussées permettent de prédire les performances acoustiques de la prothèse. Des modèles par éléments finis sont utilisés pour simuler la propagation des ondes sonores dans la prothèse et le conduit auditif. Ces simulations permettent d'optimiser le design pour obtenir la meilleure qualité sonore possible.
Des outils de réalité virtuelle sont également utilisés pour permettre au patient de visualiser et de personnaliser l'apparence de sa future prothèse. Cette approche améliore l'acceptation et la satisfaction des utilisateurs.
Processus de fabrication additive pour prothèses sur mesure
La fabrication de prothèses auditives par impression 3D suit un processus rigoureux pour garantir la qualité et la précision des appareils. Chaque étape est optimisée pour tirer le meilleur parti des technologies de fabrication additive.
Stéréolithographie (SLA) haute précision
La stéréolithographie est la technologie la plus utilisée pour imprimer les coques externes des prothèses auditives. Elle offre une excellente précision et un état de surface lisse, essentiels pour le confort du patient. Les imprimantes SLA dédiées à l'audioprothèse utilisent des résines biocompatibles spécialement formulées.
Le processus d'impression SLA pour les prothèses auditives comprend généralement les étapes suivantes :
- Préparation du fichier 3D et orientation optimale de la pièce
- Génération automatique des supports d'impression
- Impression couche par couche (épaisseur typique de 25 à 50 microns)
- Nettoyage de la pièce dans un bain de solvant
- Post-polymérisation aux UV pour finaliser les propriétés mécaniques
Des imprimantes SLA spécialisées comme la Form 3B+ de Formlabs
intègrent des fonctionnalités avancées comme le nivellement automatique du plateau ou le contrôle de la température de la résine pour garantir une qualité constante.
Frittage sélectif par laser (SLS) pour composants internes
Le frittage sélectif par laser est parfois utilisé pour fabriquer certains composants internes des prothèses auditives, comme les supports de microphones ou les canaux acoustiques. Cette technologie permet d'obtenir des pièces plus résistantes et offre une plus grande liberté de conception pour les structures internes complexes.
Le processus SLS comprend les étapes suivantes :
- Préchauffage de la poudre polymère
- Dépôt d'une fine couche de poudre (épaisseur typique de 100 microns)
- Fusion sélective de la poudre par laser
- Répétition des étapes 2 et 3 jusqu'à obtention de la pièce finale
- Refroidissement contrôlé et extraction des pièces
- Nettoyage et finition de surface
Post-traitement et finition de surface
Le post-traitement des prothèses auditives imprimées en 3D est une étape cruciale pour garantir le confort et l'esthétique des appareils. Les principales opérations de finition incluent :
- Le ponçage fin pour éliminer les marques de supports d'impression
- Le polissage pour obtenir une surface parfaitement lisse
- L'application de revêtements protecteurs ou colorés
- La stérilisation par des méthodes compatibles avec les matériaux utilisés
Des techniques avancées comme le lissage par vapeur permettent d'obtenir un état de surface optimal sans altérer la précision géométrique des pièces.
Contrôle qualité et conformité réglementaire
Chaque prothèse auditive imprimée en 3D fait l'objet d'un contrôle qualité rigoureux avant d'être livrée au patient. Des scanners 3D de haute précision sont utilisés pour vérifier la conformité dimensionnelle des pièces par rapport au modèle numérique. Des tests acoustiques et mécaniques sont également réalisés pour garantir les performances de l'appareil.
La fabrication additive de dispositifs médicaux est soumise à des réglementations strictes. Les fabricants doivent mettre en place des systèmes de gestion de la qualité conformes aux normes ISO 13485 et obtenir les certifications nécessaires auprès des autorités compétentes.
Intégration des composants électroniques miniaturisés
L'impression 3D des coques de prothèses auditives n'est qu'une partie du processus de fabrication. L'intégration des composants électroniques miniaturisés est tout aussi cruciale pour obtenir un appareil fonctionnel et performant. Les progrès dans la miniaturisation des composants permettent de créer des prothèses auditives de plus en plus discrètes et puissantes.
Les principaux composants électroniques intégrés dans une prothèse auditive moderne comprennent :
- Un ou plusieurs microphones directionnels
- Un processeur de signal numérique (DSP)
- Un amplificateur
- Un haut-parleur miniature (écouteur)
- Une batterie rechargeable ou des piles bouton
L'impression 3D permet de concevoir des logements sur mesure pour chaque composant, optimisant ainsi l'espace disponible dans la coque. Des canaux intégrés peuvent être imprimés pour le passage des fils et la gestion thermique. Certaines prothèses auditives avancées intègrent même des antennes pour la connectivité sans fil, permettant le contrôle via smartphone ou la diffusion audio directe.
La fabrication additive ouvre également la voie à l'intégration de nouveaux types de capteurs, comme des accéléromètres pour détecter les mouvements de la tête ou des capteurs optiques pour mesurer le flux sanguin dans l'oreille. Ces innovations permettent d'améliorer les performances des prothèses auditives dans diverses situations d'écoute.
Avantages cliniques et ergonomiques des prothèses imprimées en 3D
L'utilisation de l'impression 3D pour la fabrication de prothèses auditives offre de nombreux avantages cliniques et ergonomiques par rapport aux
méthodes traditionnelles. Voici les principaux bénéfices constatés :
- Un confort accru grâce à l'ajustement parfait de la coque dans le conduit auditif
- Une meilleure qualité sonore due à l'optimisation acoustique personnalisée
- Une esthétique améliorée avec des appareils plus discrets
- Une durabilité supérieure grâce aux matériaux de pointe utilisés
- Des délais de fabrication réduits, de quelques jours à quelques heures
La personnalisation poussée permise par l'impression 3D améliore significativement l'acceptation des prothèses auditives par les patients. Le taux d'abandon des appareils est réduit, ce qui se traduit par une meilleure qualité de vie pour les personnes malentendantes.
D'un point de vue clinique, la précision des prothèses imprimées en 3D permet une adaptation plus fine aux besoins auditifs spécifiques de chaque patient. Les audioprothésistes disposent d'une plus grande liberté pour ajuster la réponse en fréquence et les caractéristiques directionnelles des microphones.
Les prothèses auditives imprimées en 3D offrent une expérience auditive plus naturelle et confortable, favorisant une utilisation régulière et donc de meilleurs résultats thérapeutiques à long terme.
L'ergonomie des appareils est également améliorée. Les boutons de contrôle et les ports de charge peuvent être positionnés de manière optimale pour chaque utilisateur. L'impression 3D permet même de créer des prothèses auditives adaptées aux morphologies atypiques ou aux malformations congénitales de l'oreille.
Enfin, la rapidité de fabrication offerte par l'impression 3D permet de réaliser facilement des itérations et des ajustements. Les patients peuvent ainsi tester différentes versions de leur prothèse pour trouver la solution idéale, sans contraintes de temps ou de coût.
En conclusion, l'impression 3D révolutionne la conception et la fabrication des prothèses auditives, offrant des bénéfices tangibles tant pour les patients que pour les professionnels de santé. Cette technologie ouvre la voie à une nouvelle ère de l'audioprothèse, où chaque appareil est véritablement unique et parfaitement adapté à son utilisateur.