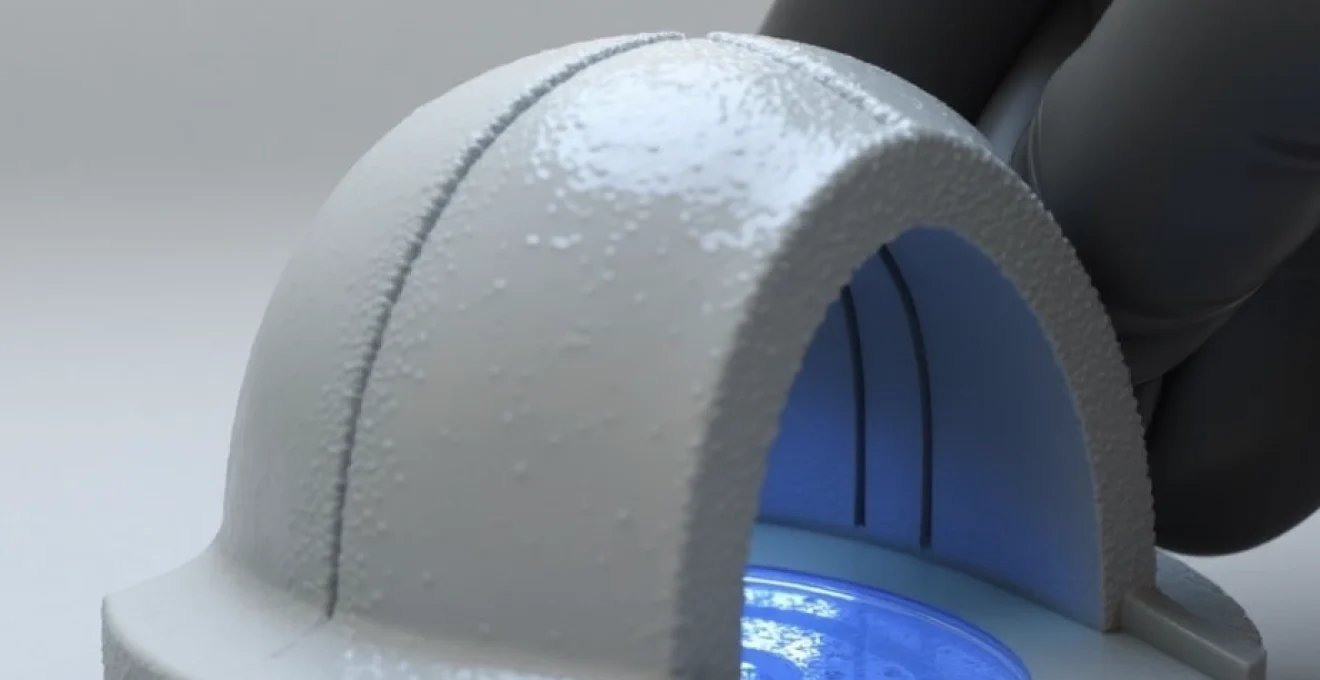
La fabrication additive, également connue sous le nom d'impression 3D, révolutionne les processus de production industrielle. Cette technologie innovante permet de créer des objets tridimensionnels en ajoutant des couches successives de matériaux, offrant une flexibilité et une personnalisation sans précédent dans la conception et la fabrication. De l'industrie automobile à l'aérospatiale, en passant par le secteur médical, la fabrication additive transforme la manière dont nous concevons, prototypons et produisons des pièces complexes. Explorons en détail les principes, les technologies et les applications de cette méthode de fabrication avant-gardiste qui redéfinit les limites de la production industrielle.
Principes fondamentaux de la fabrication additive
La fabrication additive repose sur un principe simple mais révolutionnaire : la création d'objets par ajout de matière, couche par couche, à partir d'un modèle numérique 3D. Contrairement aux méthodes de fabrication soustractive traditionnelles, comme l'usinage, qui enlèvent de la matière pour obtenir la forme désirée, la fabrication additive construit les objets de manière progressive.
Le processus commence généralement par la conception d'un modèle 3D à l'aide d'un logiciel de CAO (Conception Assistée par Ordinateur). Ce modèle est ensuite découpé en fines tranches virtuelles, chacune représentant une couche à imprimer. L'imprimante 3D lit ces données et dépose ou solidifie le matériau couche par couche, construisant progressivement l'objet final.
Cette approche offre plusieurs avantages significatifs. Tout d'abord, elle permet de créer des formes complexes et des structures internes qui seraient difficiles, voire impossibles, à réaliser avec des méthodes traditionnelles. De plus, la fabrication additive réduit considérablement les déchets de matière, car seule la quantité nécessaire est utilisée. Elle offre également une grande flexibilité en termes de personnalisation et de production à la demande, éliminant souvent le besoin de stockage de pièces de rechange.
L'un des aspects les plus prometteurs de la fabrication additive est sa capacité à optimiser topologiquement les pièces. Cette technique permet de concevoir des structures légères mais robustes, en plaçant le matériau uniquement là où il est nécessaire pour assurer la fonction et la résistance requises. Cela se traduit par des pièces plus légères, plus performantes et souvent plus économiques en termes de consommation de matière.
La fabrication additive ne se contente pas de produire des objets, elle repense fondamentalement la façon dont nous concevons et fabriquons les produits.
Technologies de dépôt de matière en fusion (FDM)
Parmi les nombreuses technologies de fabrication additive, le dépôt de matière en fusion (FDM) ou modélisation par dépôt de fil fondu est l'une des plus répandues et accessibles. Cette méthode est particulièrement appréciée pour sa simplicité, son coût relativement bas et sa capacité à produire des pièces fonctionnelles en thermoplastique.
Procédé FDM avec l'imprimante ultimaker S5
L'Ultimaker S5 est un excellent exemple d'imprimante 3D FDM de qualité professionnelle. Son fonctionnement illustre parfaitement le principe du dépôt de matière en fusion. Le matériau, sous forme de filament, est chauffé jusqu'à son point de fusion dans une buse d'extrusion. Cette buse se déplace ensuite selon les coordonnées X, Y et Z pour déposer le matériau fondu couche par couche, créant ainsi l'objet 3D.
L'Ultimaker S5 se distingue par sa double extrusion, permettant l'utilisation simultanée de deux matériaux. Cela ouvre la possibilité de créer des pièces en deux couleurs ou d'utiliser un matériau de support soluble pour des géométries complexes. Sa grande précision et sa fiabilité en font un choix privilégié pour le prototypage rapide et la production de petites séries dans divers secteurs industriels.
Matériaux thermoplastiques pour FDM : PLA, ABS, PETG
Le choix du matériau en FDM est crucial et dépend des propriétés mécaniques et thermiques recherchées pour la pièce finale. Voici les trois thermoplastiques les plus couramment utilisés :
- PLA (Acide Polylactique) : Biodégradable, facile à imprimer, idéal pour les prototypes et les objets décoratifs.
- ABS (Acrylonitrile Butadiène Styrène) : Plus résistant et durable, adapté aux pièces fonctionnelles nécessitant une bonne tenue mécanique.
- PETG (Polyéthylène Téréphtalate Glycol) : Combine la facilité d'impression du PLA avec une meilleure résistance mécanique et chimique.
Chacun de ces matériaux présente des caractéristiques uniques en termes de résistance à la température, de flexibilité et de durabilité. Le choix du matériau approprié dépendra donc de l'application spécifique de la pièce à imprimer.
Optimisation des paramètres d'impression FDM
La qualité et les propriétés mécaniques des pièces imprimées en FDM dépendent grandement des paramètres d'impression. Les principaux paramètres à optimiser incluent :
- La température d'extrusion : doit être adaptée au matériau utilisé pour assurer une fusion et une adhésion optimales.
- La vitesse d'impression : influence la précision et la qualité de surface de la pièce.
- La hauteur de couche : détermine la résolution et le temps d'impression.
- Le taux de remplissage : affecte la solidité et le poids de la pièce finale.
- L'orientation de la pièce : impacte la résistance mécanique et la qualité de surface.
L'optimisation de ces paramètres nécessite souvent une approche itérative, combinant expérience pratique et compréhension des propriétés des matériaux. Des logiciels de slicing avancés, comme Cura pour Ultimaker, offrent des profils prédéfinis et des outils d'optimisation pour faciliter ce processus.
Stéréolithographie (SLA) et traitement numérique de la lumière (DLP)
La stéréolithographie (SLA) et le traitement numérique de la lumière (DLP) sont deux technologies de fabrication additive basées sur la photopolymérisation. Ces méthodes permettent d'obtenir des pièces d'une grande précision et d'un excellent état de surface, les rendant particulièrement adaptées pour les applications nécessitant des détails fins ou une finition esthétique supérieure.
Fonctionnement de l'imprimante form 3 de formlabs
La Form 3 de Formlabs est une imprimante SLA de référence qui illustre parfaitement les avancées récentes dans cette technologie. Elle utilise un procédé appelé Low Force Stereolithography (LFS), une évolution de la SLA traditionnelle. Dans ce système, un laser UV trace chaque couche sur la surface d'un bain de résine liquide photosensible. La plateforme de construction s'abaisse progressivement, permettant à chaque nouvelle couche de se former et d'adhérer à la précédente.
L'innovation clé de la Form 3 réside dans son système optique de haute précision et sa cuve de résine flexible. Cette configuration réduit les forces exercées sur la pièce pendant l'impression, permettant d'obtenir des surfaces plus lisses et des détails plus fins, tout en améliorant la fiabilité du processus.
Résines photopolymères pour SLA : propriétés et applications
Les résines photopolymères utilisées en SLA offrent une grande variété de propriétés, adaptées à diverses applications :
- Résines standard : Idéales pour le prototypage rapide et les modèles visuels.
- Résines techniques : Offrent des propriétés mécaniques améliorées pour les pièces fonctionnelles.
- Résines biocompatibles : Certifiées pour les applications médicales et dentaires.
- Résines calcinables : Utilisées pour la fonderie de précision en joaillerie et dans l'industrie.
- Résines flexibles : Simulent les propriétés des élastomères pour des applications spécifiques.
Le choix de la résine dépend des exigences spécifiques du projet en termes de propriétés mécaniques, de résistance thermique, de biocompatibilité ou d'aspect visuel.
Post-traitement des pièces SLA : nettoyage et post-polymérisation
Contrairement à la FDM, les pièces imprimées en SLA nécessitent un post-traitement pour atteindre leurs propriétés finales. Ce processus se déroule généralement en deux étapes :
- Nettoyage : Les pièces sont lavées dans un solvant (généralement de l'alcool isopropylique) pour éliminer la résine non polymérisée de leur surface.
- Post-polymérisation : Les pièces sont exposées à une lumière UV pour compléter la polymérisation et atteindre leurs propriétés mécaniques et chimiques optimales.
Des équipements spécialisés, comme le Form Wash et le Form Cure de Formlabs, automatisent ces étapes pour assurer des résultats cohérents et de haute qualité. Le post-traitement est crucial pour garantir la stabilité dimensionnelle et les propriétés mécaniques des pièces imprimées en SLA.
Frittage sélectif par laser (SLS) pour pièces fonctionnelles
Le frittage sélectif par laser (SLS) est une technologie de fabrication additive particulièrement adaptée à la production de pièces fonctionnelles complexes. Cette méthode utilise un laser puissant pour fritter sélectivement des poudres polymères, créant des pièces solides couche par couche. Le SLS se distingue par sa capacité à produire des pièces robustes sans nécessiter de structures de support, offrant une grande liberté de conception.
Procédé SLS avec la ProX 6100 de 3D systems
La ProX 6100 de 3D Systems est une imprimante SLS industrielle qui illustre les capacités avancées de cette technologie. Son fonctionnement repose sur un processus cyclique de dépôt de poudre et de frittage laser. Un rouleau étale une fine couche de poudre polymère sur la plateforme de construction. Un laser CO2 puissant balaie ensuite la surface, fusionnant sélectivement les particules de poudre selon le motif de la couche en cours. La plateforme s'abaisse, une nouvelle couche de poudre est déposée, et le processus se répète jusqu'à ce que la pièce soit complète.
La ProX 6100 se distingue par sa grande chambre de fabrication et sa capacité à produire des pièces de haute qualité avec une excellente précision dimensionnelle. Elle est équipée de systèmes de gestion thermique avancés qui assurent une fusion homogène et des propriétés mécaniques constantes sur l'ensemble de la pièce.
Poudres polymères pour SLS : PA12, PA11, TPU
Le choix des matériaux en SLS est crucial pour obtenir les propriétés désirées dans les pièces finales. Les poudres polymères les plus couramment utilisées sont :
- PA12 (Polyamide 12) : Offre un excellent équilibre entre performances mécaniques et facilité de traitement. Idéal pour les pièces fonctionnelles et les prototypes.
- PA11 : Dérivé de sources renouvelables, il présente une meilleure élongation à la rupture et une résistance aux chocs supérieure au PA12.
- TPU (Polyuréthane Thermoplastique) : Permet de créer des pièces flexibles et élastiques, adaptées aux applications nécessitant une bonne résistance à l'usure.
Ces matériaux peuvent être enrichis d'additifs pour améliorer certaines propriétés comme la résistance à la chaleur, la conductivité électrique ou la résistance au feu, élargissant ainsi le champ des applications possibles.
Conception pour SLS : règles et bonnes pratiques
La conception pour le SLS nécessite une approche spécifique pour tirer pleinement parti des avantages de cette technologie. Voici quelques règles et bonnes pratiques essentielles :
- Épaisseur de paroi minimale : Généralement autour de 0,7 mm pour assurer la solidité de la pièce.
- Dégagement entre pièces mobiles : Un jeu minimal de 0,5 mm est recommandé pour les assemblages imprimés en une seule fois.
- Évacuation de la poudre : Prévoir des trous d'évacuation pour les cavités fermées afin de retirer la poudre non frittée.
- Orientation des pièces : Optimiser l'orientation pour minimiser la déformation et améliorer la qualité de surface.
- Structures internes : Utiliser des structures en nid d'abeille ou lattices pour alléger les pièces tout en conservant leur résistance.
En respectant ces principes, les concepteurs peuvent créer des pièces complexes et fonctionnelles qui exploitent pleinement le potentiel du SLS, comme des assemblages imbriqués ou des structures légères à haute performance.
Le SLS ouvre de nouvelles possibilités en matière de conception et de fabrication, permettant de produire des pièces qui étaient auparavant impossibles ou économiquement non viables avec les méthodes traditionnelles.
Fabrication additive métallique : SLM et EBM
La fabrication additive métallique représente une avancée majeure
dans le domaine de la production industrielle, permettant la création de pièces métalliques complexes avec des propriétés mécaniques souvent supérieures à celles obtenues par les méthodes traditionnelles. Deux technologies principales dominent ce secteur : la fusion sélective par laser (SLM) et la fusion par faisceau d'électrons (EBM).
Fusion sélective par laser (SLM) avec la M290 d'EOS
La M290 d'EOS est une machine SLM de référence dans l'industrie. Son fonctionnement repose sur l'utilisation d'un laser de haute puissance pour fondre sélectivement des particules de poudre métallique. Le processus se déroule dans une chambre sous atmosphère contrôlée, généralement remplie d'argon ou d'azote pour prévenir l'oxydation.
La M290 se distingue par sa précision et sa capacité à produire des pièces en métal dense à près de 100%. Elle offre un volume de fabrication de 250 x 250 x 325 mm, permettant la production de pièces de taille moyenne. Son système de filtration avancé assure une qualité d'atmosphère constante, essentielle pour la production de pièces de haute qualité.
Fusion par faisceau d'électrons (EBM) : spécificités et avantages
La technologie EBM, bien que moins répandue que le SLM, offre des avantages uniques pour certaines applications. Contrairement au SLM qui utilise un laser, l'EBM emploie un faisceau d'électrons pour fondre la poudre métallique. Ce processus se déroule sous vide poussé, ce qui présente plusieurs avantages :
- Absence totale d'oxydation, idéale pour les métaux réactifs comme le titane
- Températures de fabrication plus élevées, réduisant les contraintes résiduelles dans les pièces
- Vitesse de fabrication généralement plus rapide que le SLM
Cependant, l'EBM produit des pièces avec un état de surface plus rugueux que le SLM, nécessitant souvent un post-traitement plus important. Cette technologie est particulièrement adaptée à la production de pièces en titane pour les secteurs aérospatial et médical.
Alliages métalliques pour impression 3D : Ti6Al4V, inconel 718
Le choix de l'alliage métallique est crucial dans la fabrication additive métallique. Deux alliages sont particulièrement prisés pour leurs propriétés exceptionnelles :
Ti6Al4V (Titane grade 5) : Cet alliage de titane offre un excellent rapport résistance/poids, une bonne résistance à la corrosion et une biocompatibilité, le rendant idéal pour les applications aérospatiales et médicales. En fabrication additive, il permet de créer des structures légères et complexes impossibles à réaliser avec les méthodes traditionnelles.
Inconel 718 : Superalliage à base de nickel-chrome, l'Inconel 718 est reconnu pour sa résistance exceptionnelle à haute température et sa résistance à la corrosion. Il est largement utilisé dans l'industrie aérospatiale et énergétique pour la fabrication de composants de turbines et de réacteurs. La fabrication additive permet de créer des pièces en Inconel avec des géométries optimisées pour le refroidissement, améliorant ainsi les performances des moteurs.
La fabrication additive métallique ouvre la voie à une nouvelle ère de conception et de production, où la complexité n'est plus un obstacle mais une opportunité d'optimisation et d'innovation.
Applications industrielles de la fabrication additive
La fabrication additive trouve des applications dans de nombreux secteurs industriels, transformant les processus de conception, de prototypage et de production. Examinons quelques cas d'utilisation concrets dans différentes industries.
Prototypage rapide dans l'industrie automobile avec renault
Renault, comme de nombreux constructeurs automobiles, a intégré la fabrication additive dans son processus de développement de nouveaux véhicules. L'entreprise utilise principalement des technologies FDM et SLA pour le prototypage rapide de pièces intérieures et extérieures. Cette approche permet :
- Une réduction significative du temps de développement, passant de plusieurs semaines à quelques jours pour certains prototypes
- Une itération plus rapide des designs, permettant aux ingénieurs de tester et d'affiner leurs concepts
- Une réduction des coûts de développement en évitant la fabrication d'outillages coûteux pour les prototypes
Par exemple, pour le développement de la Renault Clio V, l'entreprise a utilisé l'impression 3D pour créer des maquettes à l'échelle 1:1 de certains éléments intérieurs, permettant une validation rapide de l'ergonomie et du design.
Production de pièces aérospatiales par airbus et thales
L'industrie aérospatiale est l'un des secteurs les plus avancés dans l'adoption de la fabrication additive pour la production de pièces finales. Airbus et Thales sont à l'avant-garde de cette révolution :
Airbus utilise la fabrication additive métallique (SLM et EBM) pour produire des composants structurels complexes. Un exemple notable est le support de partition de cabine pour l'A350 XWB, une pièce complexe qui était auparavant assemblée à partir de plusieurs composants. Grâce à la fabrication additive, cette pièce est maintenant produite en une seule fois, résultant en une réduction de poids de 45% et une diminution des déchets de production.
Thales Alenia Space emploie la fabrication additive pour produire des antennes et des composants de satellites. L'entreprise a notamment utilisé cette technologie pour créer des supports d'antenne en titane pour les satellites de télécommunication, réduisant le poids et le temps de production tout en améliorant les performances.
Fabrication additive dans le secteur médical : prothèses et implants
Le secteur médical bénéficie grandement de la fabrication additive, en particulier pour la production de prothèses et d'implants personnalisés. Cette technologie permet de créer des dispositifs médicaux parfaitement adaptés à l'anatomie de chaque patient, améliorant ainsi le confort et les résultats cliniques.
Un exemple marquant est la production d'implants crâniens sur mesure. Des entreprises comme Materialise utilisent des données d'imagerie médicale (scanner CT ou IRM) pour concevoir et imprimer en 3D des implants crâniens en titane parfaitement adaptés à la morphologie du patient. Cette approche réduit considérablement le temps opératoire et améliore les résultats esthétiques et fonctionnels.
Dans le domaine des prothèses, la fabrication additive permet de créer des prothèses légères et fonctionnelles, souvent à un coût inférieur aux méthodes traditionnelles. Des entreprises comme Ottobock utilisent l'impression 3D pour produire des composants de prothèses personnalisées, offrant une meilleure adaptation et un confort accru aux patients.
La fabrication additive dans le secteur médical illustre parfaitement comment cette technologie peut avoir un impact direct et positif sur la qualité de vie des individus, en permettant une personnalisation poussée des dispositifs médicaux.
En conclusion, la fabrication additive continue de transformer l'industrie, offrant de nouvelles possibilités en termes de design, de performance et de personnalisation. Du prototypage rapide à la production de pièces finales complexes, cette technologie redéfinit les limites de ce qui est possible dans la fabrication moderne. Alors que son adoption s'accélère dans divers secteurs, nous pouvons nous attendre à voir émerger des applications encore plus innovantes et transformatrices dans les années à venir.