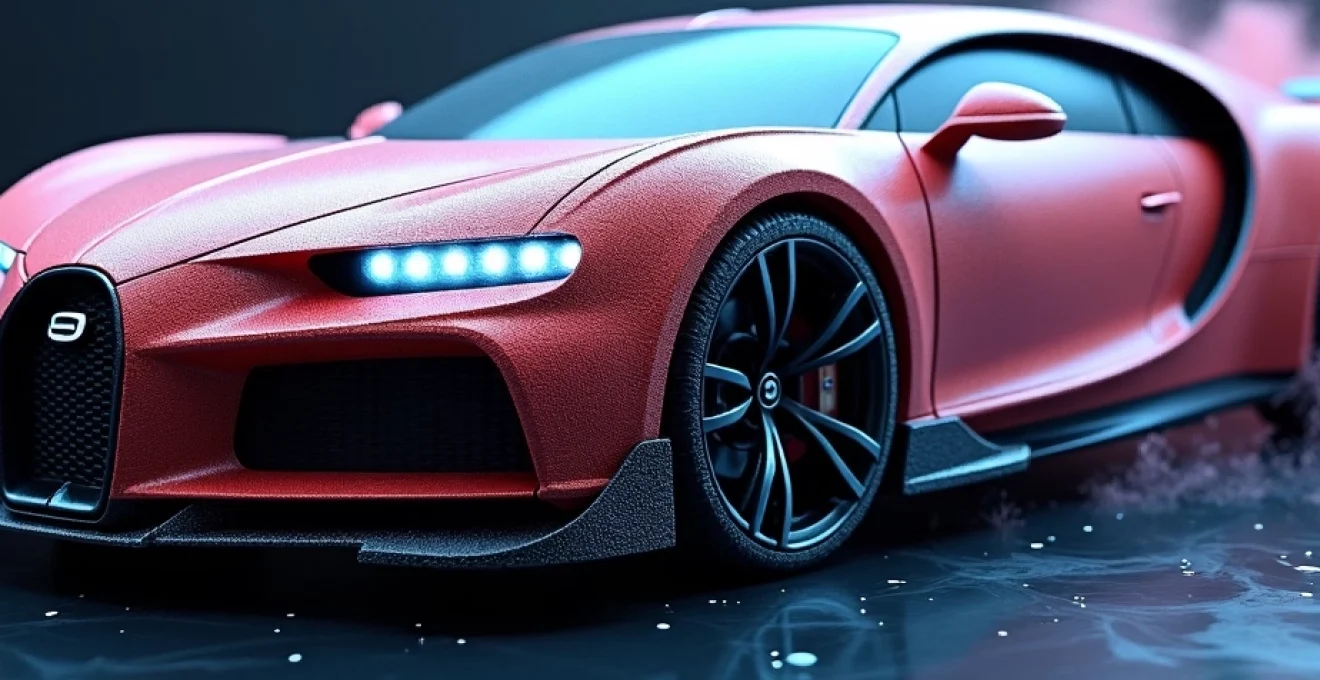
L'industrie automobile connaît une véritable révolution grâce à l'impression 3D. Cette technologie de fabrication additive transforme radicalement les processus de conception, de prototypage et de production des véhicules. Elle offre aux constructeurs une flexibilité sans précédent pour créer des pièces complexes, optimiser les performances et réduire les coûts. De la Formule 1 aux voitures de série, l'impression 3D s'impose comme un outil incontournable pour innover et rester compétitif dans un marché en constante évolution.
Technologies d'impression 3D dans l'industrie automobile
L'impression 3D regroupe plusieurs technologies distinctes, chacune présentant des avantages spécifiques pour le secteur automobile. Les constructeurs sélectionnent la méthode la plus adaptée en fonction de leurs besoins en termes de matériaux, de précision et de volume de production.
La stéréolithographie (SLA) utilise un laser pour polymériser une résine liquide couche par couche. Cette technique offre une excellente précision et un état de surface lisse, idéal pour les prototypes esthétiques et fonctionnels. Le frittage laser sélectif (SLS) fusionne des poudres de polymères ou de métaux pour créer des pièces robustes et complexes. Cette polyvalence en fait une technologie prisée pour la production de composants automobiles.
Le dépôt de fil fondu (FDM) extrude un filament thermoplastique pour construire des objets couche par couche. Simple et économique, cette méthode convient parfaitement à la réalisation de prototypes rapides et d'outillages. Enfin, la fusion laser sélective (SLM) permet d'imprimer directement des pièces métalliques haute performance, ouvrant la voie à de nouvelles possibilités en termes d'allègement et d'optimisation topologique.
Applications révolutionnaires de la fabrication additive chez les constructeurs
Les grands noms de l'automobile ont rapidement saisi le potentiel de l'impression 3D pour transformer leurs processus. Cette technologie leur permet d'accélérer l'innovation, de réduire les coûts et d'améliorer les performances de leurs véhicules. Examinons quelques exemples concrets d'applications chez les principaux constructeurs.
Prototypage rapide avec la stéréolithographie (SLA) chez renault
Renault utilise intensivement la stéréolithographie pour accélérer ses cycles de développement. Cette technologie permet au constructeur français de produire des prototypes de pièces intérieures et extérieures en quelques heures seulement. Les ingénieurs peuvent ainsi valider rapidement l'ergonomie, l'esthétique et les fonctionnalités des nouveaux composants.
La SLA offre une précision exceptionnelle, permettant de reproduire fidèlement les textures et les détails les plus fins. Renault l'emploie notamment pour prototyper des éléments de tableau de bord, des boutons de commande ou encore des grilles de calandre. Cette agilité dans le processus de conception permet à Renault d'itérer plus rapidement et d'optimiser ses designs avant la production en série.
Production de pièces fonctionnelles par frittage laser sélectif (SLS) chez BMW
BMW a franchi une étape supplémentaire en intégrant le frittage laser sélectif dans sa chaîne de production. Le constructeur allemand utilise cette technologie pour fabriquer des pièces fonctionnelles en petites et moyennes séries. La flexibilité du SLS permet de produire des géométries complexes impossibles à réaliser avec les méthodes traditionnelles.
Un exemple emblématique est la production de supports de rétroviseur pour la BMW i8 Roadster. Ces pièces allégées et optimisées topologiquement offrent une meilleure résistance tout en réduisant le poids du véhicule. BMW utilise également le SLS pour fabriquer des conduits d'aération personnalisés, améliorant ainsi l'efficacité du système de climatisation.
Fabrication de moules d'injection par dépôt de fil fondu (FDM) chez volkswagen
Volkswagen exploite le potentiel du dépôt de fil fondu pour révolutionner la fabrication de ses outillages. Le constructeur produit désormais des moules d'injection en plastique imprimés en 3D pour la production de petites séries. Cette approche réduit considérablement les coûts et les délais par rapport aux moules métalliques traditionnels.
Ces moules FDM sont particulièrement adaptés pour la production de pièces en plastique complexes, comme les grilles d'aération ou les boîtiers électroniques. Volkswagen peut ainsi répondre rapidement aux demandes de personnalisation et tester de nouveaux designs sans investissement lourd. Cette agilité est cruciale dans un marché automobile en constante évolution.
Impression métal par fusion laser sélective (SLM) pour bugatti chiron
La fusion laser sélective repousse les limites de la performance automobile chez Bugatti. Le constructeur de voitures de luxe utilise cette technologie pour produire des pièces métalliques haute performance pour sa Chiron. L'étrier de frein imprimé en 3D en titane est devenu emblématique de cette approche innovante.
Cet étrier, 40% plus léger que son équivalent en aluminium, offre une rigidité exceptionnelle grâce à sa structure optimisée. La SLM permet à Bugatti d'explorer de nouvelles géométries impossibles à réaliser avec les méthodes d'usinage classiques. Cette liberté de conception se traduit par des performances accrues et un allègement global du véhicule.
Optimisation de la chaîne logistique automobile par l'impression 3D
Au-delà de la conception et de la production, l'impression 3D transforme profondément la chaîne logistique du secteur automobile. Cette technologie offre de nouvelles opportunités pour rationaliser les stocks, réduire les délais et améliorer le service après-vente. Les constructeurs repensent leurs stratégies d'approvisionnement et de distribution grâce à ces nouvelles possibilités.
Fabrication à la demande de pièces détachées chez Mercedes-Benz
Mercedes-Benz a été pionnier dans l'utilisation de l'impression 3D pour la production de pièces détachées. Le constructeur allemand a mis en place un système de fabrication à la demande pour les pièces rares ou obsolètes de ses modèles classiques. Cette approche révolutionnaire permet de réduire considérablement les coûts de stockage et d'éliminer les problèmes d'obsolescence.
Lorsqu'un client commande une pièce spécifique, Mercedes-Benz peut désormais l'imprimer en 3D à partir des fichiers CAO originaux. Cette flexibilité garantit la disponibilité des pièces pour les véhicules anciens, prolongeant ainsi leur durée de vie et améliorant la satisfaction client. Le constructeur envisage d'étendre ce service à une gamme plus large de pièces détachées.
Réduction des stocks et délais avec la production décentralisée
L'impression 3D ouvre la voie à une production plus décentralisée, au plus proche des besoins. Les constructeurs peuvent désormais envisager d'installer des mini-usines d'impression 3D directement dans leurs concessions ou centres de distribution. Cette approche permet de réduire drastiquement les délais de livraison et les coûts de transport.
En produisant les pièces à la demande et localement, les constructeurs peuvent maintenir des stocks physiques minimaux. Cette optimisation de la chaîne logistique se traduit par une meilleure réactivité face aux fluctuations de la demande et une réduction des coûts de stockage. La production décentralisée contribue également à réduire l'empreinte carbone du secteur automobile.
Personnalisation de masse facilitée par l'impression 3D
L'impression 3D répond parfaitement aux attentes croissantes des consommateurs en matière de personnalisation. Cette technologie permet aux constructeurs de proposer des options de customisation avancées sans augmenter significativement les coûts de production. Les clients peuvent désormais choisir des finitions uniques ou des accessoires sur mesure pour leur véhicule.
Par exemple, certains constructeurs proposent déjà des éléments intérieurs personnalisés imprimés en 3D, comme des inserts de tableau de bord ou des pommeaux de levier de vitesse. Cette approche de personnalisation de masse renforce l'attachement des clients à la marque et ouvre de nouvelles opportunités commerciales pour les constructeurs.
Matériaux innovants pour l'impression 3D automobile
L'évolution rapide des matériaux d'impression 3D joue un rôle crucial dans l'adoption de cette technologie par l'industrie automobile. Les nouveaux polymères, alliages et composites offrent des propriétés mécaniques et thermiques exceptionnelles, ouvrant la voie à des applications toujours plus ambitieuses.
Polymères hautes performances ULTEM et PEEK chez ford
Ford a été l'un des premiers constructeurs à explorer le potentiel des polymères hautes performances pour l'impression 3D. Le constructeur américain utilise notamment l'ULTEM et le PEEK pour produire des pièces résistantes à la chaleur et aux produits chimiques. Ces matériaux offrent une alternative légère et durable aux métaux traditionnels.
L'ULTEM, un thermoplastique amorphe, est particulièrement apprécié pour sa résistance aux températures élevées (jusqu'à 216°C) et sa stabilité dimensionnelle. Ford l'utilise pour imprimer des composants sous capot, comme des collecteurs d'admission ou des boîtiers de filtre à air. Le PEEK, encore plus performant, trouve des applications dans les environnements les plus exigeants, comme les pièces de transmission.
Alliages légers d'aluminium et de titane pour pièces aérodynamiques
Les alliages légers imprimés en 3D révolutionnent la conception des pièces aérodynamiques. L'aluminium et le titane offrent un excellent rapport résistance/poids, permettant de créer des structures complexes et performantes. Ces matériaux sont particulièrement prisés dans le domaine de la compétition automobile.
Par exemple, certaines écuries de Formule 1 utilisent l'impression 3D d'alliages de titane pour produire des éléments aérodynamiques ultra-légers et rigides. Ces pièces optimisées topologiquement permettent d'améliorer les performances tout en respectant les contraintes réglementaires de poids. Dans le secteur de l'automobile grand public, ces alliages trouvent des applications dans la fabrication de jantes allégées ou de pièces de carrosserie haute performance.
Composites renforcés de fibres de carbone pour structures allégées
L'impression 3D de composites renforcés de fibres de carbone ouvre de nouvelles perspectives pour l'allègement des véhicules. Ces matériaux combinent la légèreté des polymères avec la résistance exceptionnelle des fibres de carbone. Les constructeurs explorent activement leur potentiel pour créer des structures automobiles plus légères et plus rigides.
Des entreprises spécialisées développent des technologies d'impression 3D capables de déposer des fibres continues de carbone dans une matrice polymère. Cette approche permet de créer des pièces structurelles optimisées, comme des renforts de châssis ou des éléments de suspension. L'utilisation de ces composites imprimés en 3D pourrait contribuer significativement à la réduction de la consommation de carburant et des émissions de CO2 des véhicules.
Défis et perspectives de l'impression 3D dans l'automobile
Malgré son potentiel révolutionnaire, l'adoption massive de l'impression 3D dans l'industrie automobile fait face à plusieurs défis. Ces obstacles techniques, réglementaires et organisationnels doivent être surmontés pour que la technologie atteigne sa pleine maturité dans le secteur.
Certification et homologation des pièces imprimées 3D
L'un des principaux freins à l'utilisation généralisée de pièces imprimées en 3D dans les véhicules de série est le processus de certification et d'homologation. Les normes actuelles, conçues pour les méthodes de fabrication traditionnelles, ne sont pas toujours adaptées aux spécificités de l'impression 3D. Les constructeurs doivent collaborer étroitement avec les autorités réglementaires pour établir de nouveaux protocoles de test et de validation.
La répétabilité et la traçabilité des pièces imprimées en 3D sont des enjeux cruciaux pour garantir leur fiabilité et leur sécurité. Des systèmes de contrôle qualité avancés, intégrant l'intelligence artificielle et l'analyse en temps réel, sont en cours de développement pour répondre à ces exigences. L'établissement de standards industriels spécifiques à l'impression 3D automobile sera déterminant pour accélérer son adoption.
Intégration dans les chaînes de production existantes
L'intégration harmonieuse de l'impression 3D dans les chaînes de production automobiles existantes représente un défi majeur. Les constructeurs doivent repenser leurs processus pour tirer pleinement parti de cette technologie sans perturber leurs opérations actuelles. Cette transition nécessite des investissements importants en équipements et en formation du personnel.
La mise en place de cellules de production hybrides , combinant impression 3D et techniques traditionnelles, semble être une approche prometteuse. Ces installations flexibles permettent d'optimiser l'utilisation de chaque technologie en fonction des besoins spécifiques de chaque pièce. L'automatisation et la robotisation joueront un rôle clé dans cette intégration, en assurant une production fluide et efficace.
Évolution des compétences et formations requises
L'adoption de l'impression 3D dans l'industrie automobile entraîne une évolution profonde des compétences requises. Les ingénieurs et techniciens doivent désormais maîtriser non seulement les principes de la conception pour la fabrication additive, mais aussi les spécificités de chaque technologie et matériau d'impression 3D.
Les constructeurs investissent massivement dans la formation de leurs équipes et collaborent avec les écoles d'ingénieurs pour adapter les cursus. De nouveaux métiers émergent, comme les designers
spécialistes en optimisation topologique pour l'impression 3D, capables d'exploiter pleinement le potentiel de cette technologie. La formation continue et l'adaptation des compétences seront essentielles pour rester compétitif dans ce domaine en constante évolution.
Les constructeurs automobiles devront également repenser leurs processus de recrutement pour attirer les talents spécialisés en fabrication additive. La collaboration avec des start-ups et des centres de recherche spécialisés permettra d'accélérer l'acquisition de ces nouvelles compétences. L'impression 3D ouvre ainsi de nouvelles perspectives professionnelles passionnantes dans le secteur automobile.
Perspectives de l'impression 3D dans l'automobile
Malgré les défis à relever, l'avenir de l'impression 3D dans l'industrie automobile s'annonce prometteur. Cette technologie est appelée à jouer un rôle toujours plus important dans la conception, la production et la maintenance des véhicules de demain. Plusieurs tendances se dessinent pour les années à venir :
- Développement de l'impression 4D, intégrant des matériaux intelligents capables de se transformer dans le temps
- Impression 3D multi-matériaux permettant de créer des pièces aux propriétés hybrides
- Intégration poussée avec l'intelligence artificielle pour optimiser la conception et la production
- Démocratisation de l'impression 3D métal pour la production en série de pièces structurelles
Ces innovations promettent de révolutionner encore davantage l'industrie automobile, en offrant des véhicules plus légers, plus performants et plus personnalisables. L'impression 3D contribuera également à rendre la production automobile plus durable, en réduisant les déchets et en facilitant le recyclage des matériaux.
En définitive, l'impression 3D s'impose comme un moteur essentiel de l'innovation dans le secteur automobile. Elle offre aux constructeurs les outils nécessaires pour relever les défis de la mobilité du futur, qu'il s'agisse de l'électrification, de l'allègement des véhicules ou de la personnalisation de masse. Les entreprises qui sauront maîtriser et intégrer pleinement cette technologie seront les mieux positionnées pour prospérer dans un marché automobile en pleine mutation.