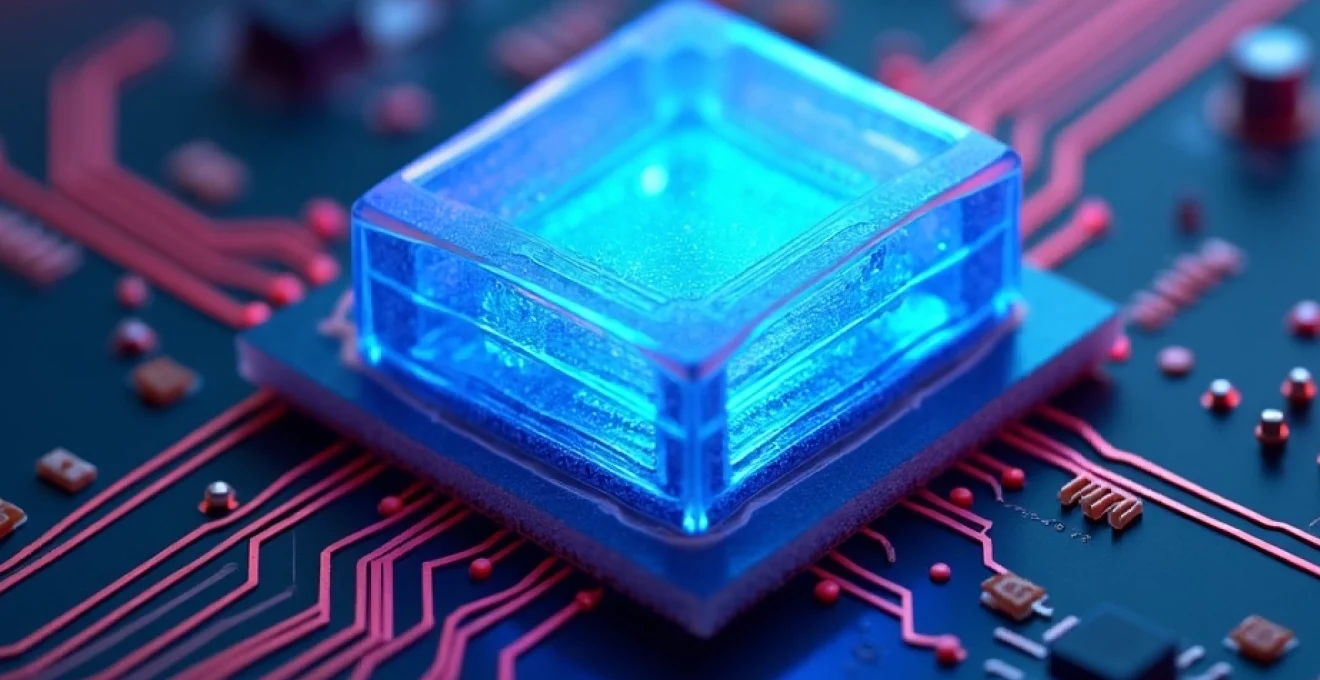
L'impression 3D révolutionne la façon dont nous concevons et fabriquons les appareils électroniques. Cette technologie offre de nouvelles possibilités en termes de personnalisation, de miniaturisation et d'intégration de fonctionnalités avancées. Des circuits imprimés aux boîtiers sur mesure, l'impression 3D transforme l'industrie électronique en permettant la création rapide de prototypes et la production de petites séries. Explorons comment cette technologie innovante façonne l'avenir des appareils électroniques et ouvre la voie à une nouvelle ère de conception et de fabrication.
Technologies de fabrication additive pour l'électronique
Plusieurs technologies d'impression 3D sont particulièrement adaptées à la fabrication de composants et d'appareils électroniques. La stéréolithographie (SLA) offre une excellente précision et des états de surface lisses, idéaux pour les boîtiers et les supports de composants. Le frittage sélectif par laser (SLS) permet quant à lui de créer des pièces fonctionnelles robustes. Pour l'électronique souple, la technologie FDM (Fused Deposition Modeling) combinée à des filaments conducteurs ouvre de nouvelles possibilités.
L'impression à jet d'encre de matériaux conducteurs est également très prometteuse pour la création directe de circuits imprimés. Cette technique permet de déposer avec précision des encres conductrices sur divers substrats, y compris flexibles. Elle offre une grande liberté de conception et la possibilité de créer des circuits 3D complexes impossibles à réaliser avec les méthodes traditionnelles.
Une autre technologie émergente est l'impression 4D, qui ajoute la dimension du temps aux objets imprimés en 3D. Des matériaux intelligents capables de changer de forme ou de propriétés en réponse à des stimuli externes ouvrent la voie à des composants électroniques auto-assemblables ou reconfigurables. Cette approche pourrait révolutionner la conception d'antennes adaptatives ou de circuits flexibles.
Matériaux conducteurs et isolants en impression 3D
Le développement de matériaux adaptés est crucial pour l'essor de l'électronique imprimée en 3D. On distingue deux grandes catégories : les matériaux conducteurs pour créer les pistes et composants électriques, et les matériaux isolants pour les structures de support et l'encapsulation. La combinaison de ces matériaux permet de créer des objets fonctionnels intégrant directement l'électronique.
Filaments composites chargés en carbone
Les filaments thermoplastiques chargés en particules conductrices comme le carbone ou le graphène offrent une conductivité électrique tout en restant compatibles avec les imprimantes 3D FDM standard. Leur résistivité peut être ajustée en fonction du taux de charge, permettant de créer aussi bien des pistes conductrices que des résistances. Ces matériaux ouvrent la voie à l'impression directe de circuits simples et de capteurs intégrés.
Résines photopolymères conductrices
Pour les technologies SLA et DLP, des résines photosensibles chargées en nanoparticules métalliques permettent d'obtenir des pièces conductrices avec une excellente résolution. Ces matériaux sont particulièrement adaptés à la création de boîtiers intégrant directement des pistes conductrices ou des antennes. Leur précision permet également de réaliser des interconnexions fines pour des composants électroniques miniaturisés.
Poudres métalliques pour frittage laser
Le frittage laser de poudres métalliques comme le cuivre ou l'argent permet de créer directement des composants conducteurs massifs. Cette technique est idéale pour fabriquer des dissipateurs thermiques, des blindages électromagnétiques ou des électrodes complexes. La densité et la conductivité des pièces obtenues se rapprochent de celles des métaux usinés traditionnellement.
Encres conductrices pour impression à jet d'encre
Les encres conductrices à base de nanoparticules métalliques ou de polymères conducteurs révolutionnent la fabrication de circuits imprimés. Déposées par jet d'encre sur divers substrats, elles permettent de créer rapidement des prototypes de PCB ou des antennes flexibles. Leur compatibilité avec des supports souples ouvre la voie à l'électronique portable et aux wearables .
Applications de l'impression 3D dans l'industrie électronique
L'impression 3D transforme de nombreux aspects de la conception et de la fabrication d'appareils électroniques. Du prototypage rapide à la production personnalisée, cette technologie offre de nouvelles possibilités aux ingénieurs et aux fabricants. Examinons quelques applications concrètes qui illustrent le potentiel de l'impression 3D dans ce domaine.
Prototypage rapide de PCB avec voltera V-One
Le prototypage de circuits imprimés est l'une des applications les plus prometteuses de l'impression 3D en électronique. Des systèmes comme le Voltera V-One permettent de créer des PCB fonctionnels en quelques heures, directement sur le bureau de l'ingénieur. Cette approche accélère considérablement les cycles de conception et réduit les coûts de développement.
Le processus est simple : le circuit est d'abord imprimé avec une encre conductrice, puis les composants sont placés et soudés. Des vias peuvent être créés pour les connexions multicouches. Cette technique permet de tester rapidement de nouvelles idées et d'itérer sur les conceptions avant de passer à la production en série.
"Le prototypage rapide de PCB par impression 3D a réduit nos cycles de développement de plusieurs semaines à quelques jours. C'est un game-changer pour l'innovation en électronique."
Fabrication de boîtiers sur mesure pour appareils IoT
L'Internet des Objets (IoT) nécessite souvent des appareils compacts avec des formes spécifiques adaptées à leur environnement. L'impression 3D est idéale pour créer rapidement des boîtiers personnalisés intégrant directement les fixations, les passages de câbles et les ouvertures pour les capteurs. Cette flexibilité permet d'optimiser l'ergonomie et l'esthétique des produits tout en réduisant les coûts de développement.
De plus, l'impression 3D permet de produire économiquement de petites séries, parfaites pour les phases de test ou les marchés de niche. Les matériaux comme l'ABS ou le nylon offrent une bonne résistance mécanique et peuvent intégrer des additifs pour la protection UV ou la résistance au feu, répondant ainsi aux exigences des appareils IoT destinés à un usage extérieur.
Impression d'antennes RFID flexibles
La technologie RFID est omniprésente dans notre quotidien, des cartes de transport aux étiquettes anti-vol. L'impression 3D permet de créer des antennes RFID flexibles et personnalisées, ouvrant la voie à de nouvelles applications. En utilisant des encres conductrices sur des substrats souples, il est possible d'imprimer des antennes directement sur des emballages ou des vêtements.
Cette approche offre plusieurs avantages :
- Personnalisation facile de la forme et des caractéristiques de l'antenne
- Réduction des coûts pour les petites séries
- Intégration possible dans des objets aux formes complexes
- Fabrication à la demande, réduisant les stocks
L'impression d'antennes RFID flexibles ouvre de nouvelles perspectives pour la traçabilité des produits, l'authentification et les paiements sans contact.
Création de capteurs intégrés par multi-matériaux
L'impression 3D multi-matériaux permet de créer des objets combinant des parties conductrices et isolantes en une seule opération. Cette technique est particulièrement intéressante pour la fabrication de capteurs intégrés directement dans la structure des objets. Par exemple, il est possible d'imprimer un boîtier en plastique avec des pistes conductrices et des zones sensibles à la pression ou à la température.
Ces capteurs intégrés trouvent des applications dans divers domaines :
- Prothèses intelligentes avec retour tactile
- Emballages connectés pour le suivi de la chaîne du froid
- Vêtements techniques pour le sport ou la santé
- Interfaces homme-machine ergonomiques
La possibilité de créer des objets "intelligents" en une seule étape de fabrication ouvre la voie à une nouvelle génération de produits électroniques plus intégrés et fonctionnels.
Défis techniques de l'électronique imprimée en 3D
Malgré ses nombreux avantages, l'électronique imprimée en 3D fait face à plusieurs défis techniques qui doivent être surmontés pour une adoption plus large. Ces obstacles concernent principalement la précision, la fiabilité et les performances des composants imprimés.
Résolution et précision des imprimantes FDM vs SLA
La résolution d'impression est cruciale pour la création de circuits électroniques fonctionnels. Les imprimantes FDM (Fused Deposition Modeling) offrent une bonne polyvalence et un coût accessible, mais leur résolution est généralement limitée à environ 100 microns. Cette précision est suffisante pour des circuits simples, mais peut poser problème pour des designs plus complexes.
En revanche, les imprimantes SLA (stéréolithographie) atteignent des résolutions de l'ordre de 25 microns, permettant la création de pistes conductrices plus fines et précises. Cependant, les matériaux SLA conducteurs sont encore en développement et présentent souvent des propriétés électriques inférieures à celles des encres conductrices traditionnelles.
Technologie | Résolution typique | Avantages | Inconvénients |
---|---|---|---|
FDM | 100-200 µm | Coût accessible, large gamme de matériaux | Résolution limitée, état de surface moyen |
SLA | 25-50 µm | Haute précision, bon état de surface | Matériaux conducteurs limités, post-traitement nécessaire |
Adhésion entre couches conductrices et isolantes
L'un des défis majeurs de l'électronique imprimée en 3D est d'assurer une bonne adhésion entre les matériaux conducteurs et isolants. Une mauvaise adhésion peut entraîner des délaminations, des fissures ou des court-circuits, compromettant la fiabilité du dispositif. Ce problème est particulièrement critique pour les objets flexibles ou soumis à des contraintes mécaniques.
Plusieurs approches sont explorées pour améliorer l'adhésion :
- Développement de matériaux compatibles avec des interfaces optimisées
- Utilisation de couches d'accroche ou de promoteurs d'adhésion
- Modification de surface par plasma ou traitement chimique
- Conception de structures mécaniques favorisant l'ancrage entre couches
La résolution de ce défi est essentielle pour garantir la durabilité et la fiabilité des dispositifs électroniques imprimés en 3D.
Gestion thermique des composants électroniques imprimés
La dissipation thermique est un aspect crucial de la conception électronique, particulièrement pour les composants de puissance. Les matériaux plastiques couramment utilisés en impression 3D ont généralement une faible conductivité thermique, ce qui peut limiter les performances des dispositifs imprimés.
Pour surmonter ce problème, plusieurs stratégies sont mises en œuvre :
- Utilisation de matériaux composites chargés en particules conductrices thermiques
- Conception de structures optimisées pour la dissipation (ailettes, canaux de refroidissement)
- Intégration de zones métalliques imprimées en 3D pour l'évacuation de la chaleur
- Combinaison de l'impression 3D avec des dissipateurs thermiques traditionnels
La gestion efficace de la thermique est essentielle pour permettre l'impression 3D de composants électroniques plus performants et fiables.
Avenir de l'électronique imprimée en 4D
L'impression 4D, extension de l'impression 3D intégrant la dimension temporelle, ouvre de nouvelles perspectives fascinantes pour l'électronique. Cette technologie permet de créer des objets capables de changer de forme ou de propriétés en réponse à des stimuli externes comme la chaleur, l'humidité ou un champ électrique. Appliquée à l'électronique, l'impression 4D pourrait révolutionner la conception de dispositifs adaptatifs et auto-reconfigurables.
Matériaux à mémoire de forme pour circuits auto-assemblables
Les matériaux à mémoire de forme sont au cœur de l'électronique 4D. Ces polymères ou alliages métalliques peuvent être programmés pour changer de forme de manière prédéfinie en réponse à un stimulus. Dans le contexte de l'électronique, cela ouvre la voie à des circuits imprimés en 3D qui peuvent s'auto-assembler ou se reconfigurer.
Imaginez un circuit imprimé plat qui se transforme en une structure 3D complexe lorsqu'il est chauffé, créant ainsi des connexions électriques et des dispositifs impossibles à fabriquer directement. Cette approche pourrait révolutionner la conception d'antennes adaptatives, de capteurs déployables pour l'exploration spatiale, ou encore d'implants médicaux auto-ajustables.
"L'électronique 4
D est sur le point de transformer radicalement la conception et la fabrication de composants électroniques." - Dr. Jennifer Lewis, Harvard University
Impression de batteries flexibles et étirables
L'impression 3D ouvre également de nouvelles possibilités pour la fabrication de batteries flexibles et étirables, essentielles pour les appareils électroniques portables et l'électronique souple. Des chercheurs ont développé des encres conductrices à base de nanoparticules qui peuvent être imprimées en couches pour former des batteries souples.
Ces batteries imprimées en 3D présentent plusieurs avantages :
- Adaptabilité à des formes complexes et ergonomiques
- Possibilité d'intégration directe dans les objets lors de leur fabrication
- Personnalisation facile de la capacité et des dimensions
- Réduction potentielle des coûts pour les petites séries
Bien que les performances de ces batteries soient encore inférieures à celles des batteries lithium-ion traditionnelles, elles ouvrent la voie à une nouvelle génération d'appareils électroniques conformables et étirables. Des applications dans les textiles intelligents, les capteurs biomédicaux ou les écrans flexibles sont envisagées.
Intégration de nanotubes de carbone pour l'électronique souple
Les nanotubes de carbone (NTC) sont des structures cylindriques de carbone aux propriétés électriques et mécaniques exceptionnelles. Leur intégration dans les matériaux d'impression 3D ouvre de nouvelles perspectives pour l'électronique souple et les capteurs haute performance.
Les avantages des NTC pour l'électronique imprimée en 3D incluent :
- Conductivité électrique élevée même sous étirement
- Excellente résistance mécanique et flexibilité
- Stabilité thermique et chimique
- Possibilité de créer des composants semi-conducteurs
Des chercheurs ont déjà démontré la fabrication de transistors flexibles, de capteurs de pression et d'électrodes transparentes en utilisant des encres chargées en NTC. Ces avancées pourraient révolutionner des domaines tels que l'électronique portable, les interfaces homme-machine ou les prothèses intelligentes.
Cependant, des défis subsistent, notamment la dispersion homogène des NTC dans les matrices polymères et le contrôle précis de leurs propriétés électroniques. La recherche se poursuit pour optimiser les formulations d'encre et les procédés d'impression afin d'exploiter pleinement le potentiel des nanotubes de carbone en électronique imprimée.
En conclusion, l'impression 3D et 4D ouvre des perspectives fascinantes pour l'avenir de l'électronique. Des circuits auto-assemblables aux batteries flexibles en passant par l'intégration de nanomatériaux, ces technologies promettent de transformer radicalement la conception et la fabrication des appareils électroniques. Bien que des défis techniques subsistent, les progrès rapides dans ce domaine laissent entrevoir un futur où l'électronique sera plus intégrée, adaptative et personnalisable que jamais.