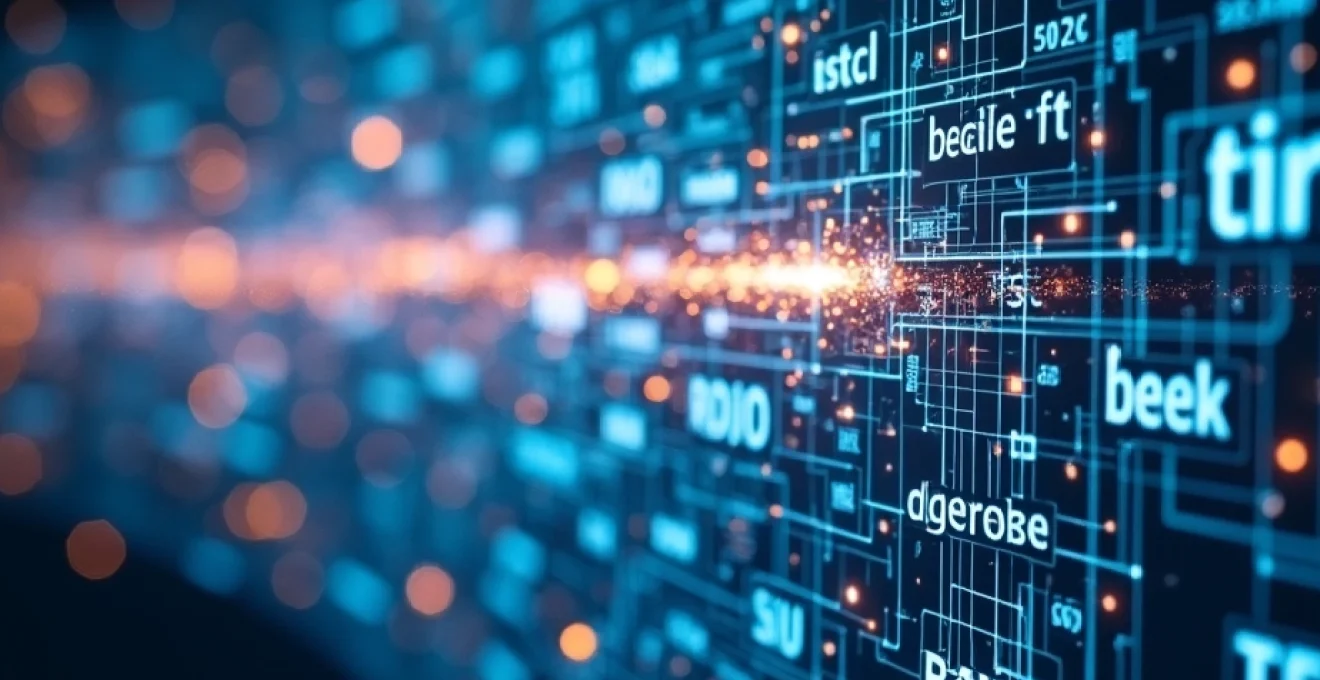
Dans le monde industriel moderne, la production de haute qualité est devenue un impératif stratégique pour les entreprises manufacturières. Elle représente bien plus qu'une simple exigence technique ; c'est un véritable pilier de la compétitivité et de la pérennité des organisations. Face à des marchés de plus en plus exigeants et une concurrence globalisée, les industriels doivent constamment repousser les limites de l'excellence opérationnelle. Cette quête permanente de la qualité implique l'adoption de méthodologies avancées, l'intégration de technologies de pointe et le développement continu des compétences. Explorons ensemble les éléments clés qui permettent d'atteindre et de maintenir une production de haute qualité dans l'industrie d'aujourd'hui.
Méthodologies de production industrielle de pointe
Les méthodologies de production industrielle avancées constituent le socle d'une fabrication de haute qualité. Ces approches systématiques permettent d'optimiser les processus, de réduire les gaspillages et d'améliorer continuellement la performance. Parmi les plus efficaces, on retrouve le Lean Manufacturing, le Six Sigma et l'Agile Manufacturing. Ces méthodes ne sont pas mutuellement exclusives ; au contraire, leur combinaison judicieuse peut créer des synergies puissantes.
Le Lean Manufacturing, issu du Toyota Production System, se concentre sur l'élimination des activités sans valeur ajoutée. Cette approche vise à fluidifier les flux de production et à réduire les stocks intermédiaires. Le Six Sigma, quant à lui, met l'accent sur la réduction de la variabilité des processus pour atteindre un niveau de qualité proche de la perfection. L'Agile Manufacturing, plus récente, apporte une flexibilité accrue pour s'adapter rapidement aux changements du marché.
L'adoption de ces méthodologies requiert un engagement fort de la direction et une transformation culturelle de l'entreprise. Il ne s'agit pas simplement d'appliquer des outils, mais de repenser en profondeur la manière dont l'organisation fonctionne. Cette démarche implique souvent une refonte des processus, une réorganisation des équipes et un investissement dans la formation du personnel.
Systèmes de gestion de la qualité pour l'excellence manufacturière
Les systèmes de gestion de la qualité (SGQ) jouent un rôle crucial dans la production de haute qualité. Ils fournissent un cadre structuré pour organiser, planifier et contrôler toutes les activités liées à la qualité au sein de l'entreprise. Un SGQ efficace permet non seulement d'assurer la conformité des produits aux spécifications, mais aussi d'améliorer continuellement les processus et la satisfaction client.
Mise en œuvre de la norme ISO 9001:2015 dans les processus de production
La norme ISO 9001:2015 est reconnue mondialement comme le standard de référence pour les systèmes de gestion de la qualité. Sa mise en œuvre dans les processus de production apporte une rigueur et une cohérence essentielles à l'atteinte de hauts niveaux de qualité. Cette norme adopte une approche basée sur les risques, encourageant les entreprises à anticiper les problèmes potentiels plutôt que de simplement réagir aux non-conformités.
L'un des aspects clés de l'ISO 9001:2015 est l'accent mis sur le leadership et l'engagement de la direction. Cette implication au plus haut niveau est cruciale pour insuffler une véritable culture de la qualité dans toute l'organisation. La norme encourage également une approche processus, qui permet de mieux comprendre et gérer les interactions entre les différentes activités de l'entreprise.
Application du lean manufacturing pour optimiser les flux de production
Le Lean Manufacturing est une méthodologie puissante pour optimiser les flux de production et éliminer les gaspillages. Son application permet de réduire les temps de cycle, d'améliorer la qualité et de diminuer les coûts. Les principes clés du Lean incluent la valeur , le flux , la demande , la perfection et le respect des personnes .
L'un des outils emblématiques du Lean est le Value Stream Mapping
(VSM), qui permet de visualiser l'ensemble du flux de valeur et d'identifier les opportunités d'amélioration. D'autres techniques comme le 5S
, le Kanban
ou le SMED
(Single-Minute Exchange of Die) contribuent à créer un environnement de travail plus efficace et à réduire les temps de changement de série.
L'application rigoureuse des principes du Lean Manufacturing peut conduire à des gains de productivité de 20 à 30% dans de nombreuses industries.
Intégration du total quality management (TQM) dans la culture d'entreprise
Le Total Quality Management (TQM) est une approche globale de la gestion de la qualité qui implique tous les niveaux de l'organisation. Son intégration dans la culture d'entreprise est essentielle pour atteindre une production de haute qualité durable. Le TQM repose sur plusieurs principes fondamentaux, dont l'orientation client, l'amélioration continue et l'implication totale du personnel.
La mise en place du TQM nécessite un changement de mentalité à tous les niveaux de l'entreprise. Il s'agit de passer d'une approche réactive à une approche proactive de la qualité. Cela implique de former et de responsabiliser les employés, de favoriser la communication transversale et de mettre en place des systèmes de mesure et de feedback efficaces.
Technologies avancées pour la production de haute précision
L'avènement de l'Industrie 4.0 a apporté une multitude de technologies avancées qui révolutionnent la production de haute précision. Ces innovations permettent d'atteindre des niveaux de qualité et de reproductibilité inégalés, tout en offrant une flexibilité accrue et une réduction des coûts. Explorons quelques-unes de ces technologies clés.
Usinage CNC 5 axes pour composants complexes
L'usinage CNC 5 axes représente une avancée majeure dans la fabrication de composants complexes. Cette technologie permet de réaliser des pièces avec une précision extrême, en accédant à des géométries auparavant impossibles à atteindre. Les machines 5 axes peuvent travailler simultanément selon trois axes linéaires et deux axes rotatifs, offrant une liberté de mouvement sans précédent.
Les avantages de l'usinage 5 axes sont nombreux :
- Réduction du nombre de montages, diminuant ainsi les risques d'erreur
- Amélioration de la qualité de surface et de la précision dimensionnelle
- Possibilité de réaliser des formes complexes en une seule opération
- Augmentation de la productivité grâce à des temps d'usinage réduits
Cette technologie trouve des applications dans des secteurs exigeants comme l'aérospatiale, l'automobile ou le médical, où la précision est critique.
Fabrication additive métallique pour prototypage rapide
La fabrication additive métallique, également connue sous le nom d'impression 3D métallique, révolutionne le prototypage rapide et la production de petites séries. Cette technologie permet de créer des pièces complexes directement à partir de fichiers CAO, en déposant et fusionnant des couches successives de poudre métallique.
Les avantages de la fabrication additive métallique sont nombreux :
- Réduction drastique des délais de prototypage
- Possibilité de réaliser des géométries impossibles avec les méthodes traditionnelles
- Optimisation topologique pour réduire le poids des pièces
- Personnalisation poussée sans surcoût de production
Cette technologie ouvre de nouvelles perspectives dans la conception de produits, permettant d'explorer des solutions innovantes et d'optimiser les performances des pièces.
Métrologie 3D et contrôle qualité automatisé
La métrologie 3D et le contrôle qualité automatisé sont devenus des éléments incontournables dans la production de haute qualité. Les systèmes de mesure tridimensionnelle, tels que les machines à mesurer tridimensionnelles (MMT) ou les scanners 3D, permettent de vérifier avec une précision extrême la conformité des pièces produites.
L'automatisation du contrôle qualité apporte plusieurs avantages :
- Augmentation de la fiabilité et de la répétabilité des mesures
- Réduction des temps de contrôle et augmentation de la productivité
- Détection précoce des dérives de production
- Traçabilité accrue grâce à l'enregistrement automatique des données de mesure
Ces technologies permettent non seulement de garantir la qualité des produits, mais aussi d'alimenter des boucles de rétroaction pour l'amélioration continue des processus.
Robotique collaborative dans les lignes d'assemblage
La robotique collaborative, ou cobotique , représente une évolution majeure dans l'automatisation des lignes d'assemblage. Contrairement aux robots industriels traditionnels, les cobots sont conçus pour travailler en interaction directe avec les opérateurs humains, combinant ainsi la flexibilité humaine et la précision robotique.
Les avantages de la robotique collaborative sont multiples :
- Amélioration de la qualité et de la constance des opérations d'assemblage
- Réduction de la fatigue et des troubles musculo-squelettiques chez les opérateurs
- Flexibilité accrue permettant de s'adapter rapidement aux changements de production
- Optimisation de l'espace de travail grâce à l'absence de barrières de sécurité
L'intégration de cobots dans les lignes d'assemblage permet d'atteindre un nouvel équilibre entre automatisation et intervention humaine, contribuant ainsi à une production de haute qualité.
Traçabilité et gestion des données de production
Dans un contexte de production de haute qualité, la traçabilité et la gestion efficace des données de production sont devenues des enjeux majeurs. Ces aspects permettent non seulement de garantir la conformité réglementaire, mais aussi d'optimiser les processus et de réagir rapidement en cas de problème.
Mise en place de systèmes MES (manufacturing execution system)
Les systèmes MES (Manufacturing Execution System) jouent un rôle central dans la gestion des données de production. Ils assurent le lien entre les systèmes de planification (ERP) et les équipements de production, permettant une supervision en temps réel de l'atelier. Un MES performant collecte, analyse et restitue les données de production, offrant ainsi une visibilité totale sur les opérations.
Les fonctionnalités clés d'un système MES incluent :
- Ordonnancement et suivi de la production
- Gestion de la qualité et des non-conformités
- Traçabilité des lots et des composants
- Analyse des performances (OEE, KPI)
- Gestion de la maintenance
La mise en place d'un MES permet d'améliorer significativement la réactivité et l'efficacité de la production, contribuant ainsi à l'atteinte d'un haut niveau de qualité.
Utilisation de l'IoT industriel pour la surveillance en temps réel
L'Internet des Objets (IoT) industriel révolutionne la manière dont les entreprises surveillent et contrôlent leurs opérations de production. En connectant les machines, les capteurs et les systèmes, l'IoT industriel permet une collecte et une analyse en temps réel des données de production.
Les avantages de l'IoT industriel pour la qualité sont nombreux :
- Détection précoce des anomalies et prévention des défauts
- Optimisation des paramètres de production en temps réel
- Traçabilité fine des conditions de fabrication de chaque lot
- Amélioration de la maintenance prédictive
L'adoption de l'IoT industriel peut conduire à une réduction de 20% des temps d'arrêt non planifiés et à une augmentation de 10% de la productivité.
Analyse prédictive pour la maintenance et l'optimisation des processus
L'analyse prédictive, basée sur l'exploitation des données massives ( Big Data ) et l'intelligence artificielle, ouvre de nouvelles perspectives pour la maintenance et l'optimisation des processus. En analysant les tendances et les corrélations dans les données historiques, il devient possible d'anticiper les problèmes avant qu'ils ne surviennent et d'optimiser en continu les paramètres de production.
Les applications de l'analyse prédictive incluent :
- La maintenance prédictive, permettant de planifier les interventions au moment optimal
- L'optimisation des paramètres de production pour maximiser la qualité et le rendement
- La prévision des défauts de qualité basée sur l'analyse des données de production
- L'amélioration continue des processus grâce à l'identification des facteurs clés de performance
L'intégration de l'analyse prédictive dans les processus de production contribue à une amélioration significative de la qualité et de l'efficacité opérationnelle.
Formation et développement des compétences pour la haute qualité
La production de haute qualité repose en grande partie sur les compétences et l'engagement des équipes. Dans un environnement industriel en constante évolution, la formation continue et le développement des compétences sont devenus des impératifs stratégiques. Les entreprises doivent investir dans leur capital humain pour rester compétitives et maintenir un haut niveau de qualité.
Les principales stratégies de formation et développement des compétences pour la haute qualité incluent :
- La formation continue aux nouvelles technologies et méthodologies
- Le développement des soft skills comme la résolution de problèmes et le travail d'équipe
- La mise en place de programmes de mentorat et de partage des connaissances
- L'utilisation de la réalité virtuelle et augmentée pour la formation pratique
- L'évaluation régulière des compétences et l'élaboration de plans de développement personnalisés
L'investissement dans la formation ne doit pas être vu comme un coût, mais comme un levier essentiel de performance et de qualité. Les entreprises qui mettent l'accent sur le développement continu de leurs équipes sont mieux armées pour relever les défis de l'industrie moderne.
Certification et conformité aux normes internationales de production
La certification et la conformité aux normes internationales jouent un rône crucial dans la production de haute qualité. Elles permettent non seulement de garantir la qualité des produits, mais aussi d'accéder à de nouveaux marchés et de renforcer la confiance des clients.
Parmi les principales certifications et normes relatives à la qualité de production, on peut citer :
- ISO 9001 pour les systèmes de management de la qualité
- IATF 16949 pour l'industrie automobile
- AS9100 pour l'aérospatiale
- ISO 13485 pour les dispositifs médicaux
- ISO 22000 pour la sécurité des denrées alimentaires
L'obtention et le maintien de ces certifications nécessitent un engagement fort de l'entreprise et la mise en place de processus rigoureux. Cependant, les bénéfices en termes de qualité, d'efficacité et de reconnaissance sur le marché sont indéniables.
Les entreprises certifiées ISO 9001 affichent en moyenne une augmentation de 50% de leur productivité et une réduction de 65% des réclamations clients.
Au-delà des certifications générales, de nombreuses industries ont développé leurs propres standards spécifiques. Par exemple, l'industrie pharmaceutique suit les Bonnes Pratiques de Fabrication (BPF), tandis que l'électronique adhère aux normes IPC pour la fabrication des circuits imprimés.
La conformité à ces normes implique souvent des audits réguliers, internes et externes, pour s'assurer du respect continu des exigences. Ces audits sont l'occasion d'identifier des opportunités d'amélioration et de maintenir une dynamique de progrès.
En conclusion, la production de haute qualité est un défi complexe qui nécessite une approche holistique. Elle repose sur l'intégration de méthodologies avancées, l'adoption de technologies de pointe, une gestion efficace des données, le développement continu des compétences et le respect des normes internationales. Les entreprises qui réussissent à maîtriser ces différents aspects sont celles qui se distinguent sur des marchés de plus en plus exigeants et compétitifs.
Dans un monde en constante évolution, la quête de la qualité est un processus sans fin. Les industriels doivent rester à l'affût des nouvelles tendances et innovations pour continuer à repousser les limites de l'excellence. La production de haute qualité n'est pas seulement un objectif, c'est un voyage continu vers la perfection.