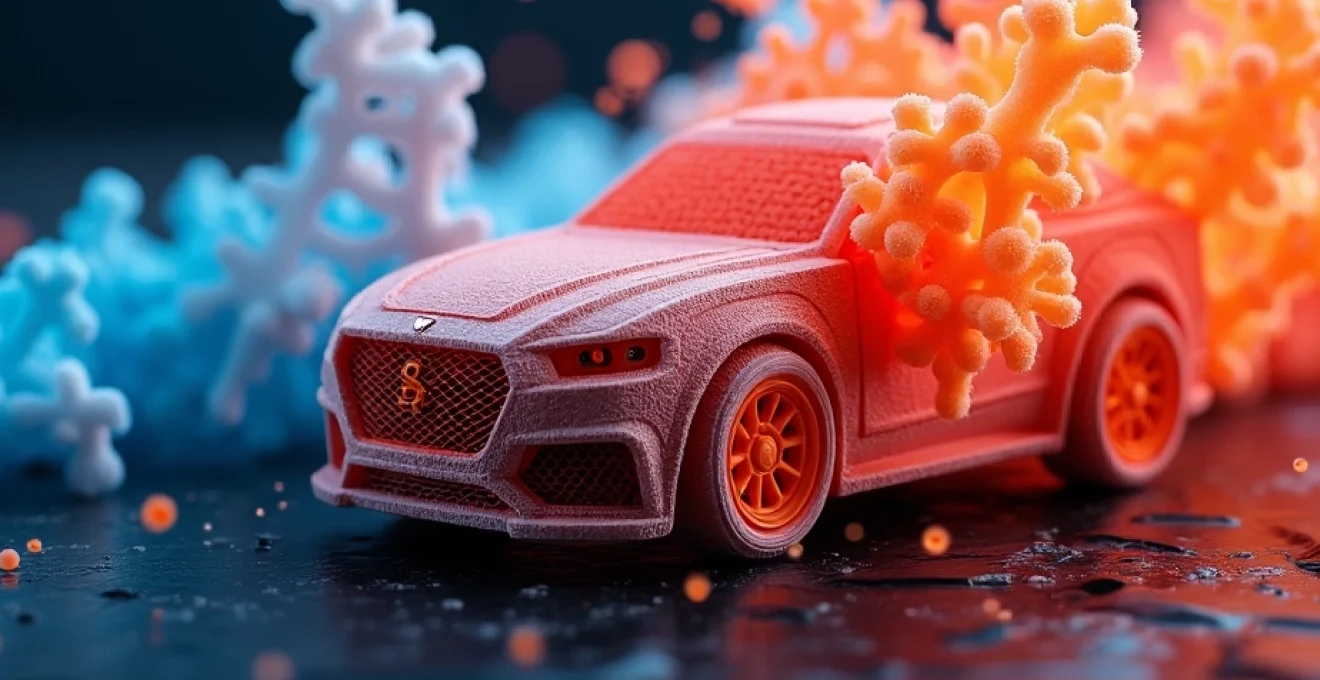
L'impression 3D révolutionne de nombreux secteurs industriels, offrant de nouvelles possibilités en termes de conception, de personnalisation et d'efficacité de production. Cette technologie de fabrication additive permet de créer des objets tridimensionnels couche par couche, ouvrant la voie à des innovations dans des domaines aussi variés que la médecine, l'aérospatiale ou l'automobile. Son adoption croissante transforme les processus de fabrication traditionnels et repousse les limites de ce qu'il est possible de produire. Explorons comment différentes industries tirent parti de l'impression 3D pour innover et optimiser leurs activités.
Révolution manufacturière par l'impression 3D
L'impression 3D bouleverse les méthodes de production traditionnelles dans de nombreux secteurs industriels. Cette technologie permet de fabriquer des pièces complexes en une seule étape, réduisant ainsi les coûts et les délais de production. Elle offre également une grande flexibilité, permettant de produire des petites séries ou des pièces uniques de manière rentable.
Dans l'industrie manufacturière, l'impression 3D est utilisée pour le prototypage rapide, la fabrication d'outillages et la production de pièces finales. Elle permet aux entreprises d'itérer rapidement sur leurs conceptions, de tester différentes versions et d'optimiser leurs produits avant la production en série. Cette agilité accrue réduit considérablement le temps de mise sur le marché de nouveaux produits.
Un des principaux avantages de l'impression 3D est la possibilité de créer des géométries complexes impossibles à réaliser avec les méthodes de fabrication traditionnelles. Cela ouvre la voie à des designs innovants et à l'optimisation topologique des pièces, permettant de réduire leur poids tout en conservant leurs propriétés mécaniques. Cette caractéristique est particulièrement intéressante pour les industries aéronautique et automobile, toujours à la recherche d'allègement des structures.
L'impression 3D permet également de réduire les déchets de production. Contrairement à l'usinage qui enlève de la matière, la fabrication additive n'utilise que la quantité de matériau nécessaire. Cela en fait une technologie plus durable et économe en ressources. De plus, la possibilité de produire localement réduit les besoins en transport et les émissions associées.
Applications médicales avancées de la fabrication additive
Le secteur médical est l'un des domaines où l'impression 3D a le plus d'impact, offrant de nouvelles possibilités pour améliorer les soins aux patients. Cette technologie permet de créer des dispositifs médicaux personnalisés, des prothèses sur mesure et même des tissus vivants.
Prothèses et implants personnalisés par CAO/FAO
L'impression 3D révolutionne la fabrication de prothèses et d'implants en permettant une personnalisation poussée. Grâce à l'utilisation de scanners 3D et de logiciels de conception assistée par ordinateur (CAO), il est possible de créer des prothèses parfaitement adaptées à l'anatomie de chaque patient. Cette approche améliore considérablement le confort et la fonctionnalité des prothèses, qu'il s'agisse de membres artificiels ou d'implants dentaires.
Les implants crâniens et maxillo-faciaux bénéficient particulièrement de cette technologie. Des implants sur mesure peuvent être conçus pour remplacer des parties osseuses endommagées ou manquantes, offrant des résultats esthétiques et fonctionnels supérieurs aux solutions standard. L'impression 3D permet également de produire des guides chirurgicaux personnalisés qui aident les chirurgiens à positionner précisément les implants pendant l'opération.
Bio-impression de tissus et organes fonctionnels
La bio-impression 3D est l'une des applications les plus prometteuses et révolutionnaires de la fabrication additive dans le domaine médical. Cette technologie consiste à imprimer des tissus vivants en déposant couche par couche des cellules et des matériaux de support. L'objectif ultime est de pouvoir créer des organes fonctionnels pour la transplantation, répondant ainsi à la pénurie chronique de donneurs.
Bien que la création d'organes complexes reste un défi, des progrès significatifs ont déjà été réalisés. Des chercheurs ont réussi à imprimer des structures tissulaires simples comme des vaisseaux sanguins et des fragments de peau. Ces tissus imprimés en 3D peuvent être utilisés pour tester des médicaments, réduisant ainsi le besoin d'expérimentation animale. À terme, la bio-impression pourrait révolutionner la médecine régénérative en permettant la fabrication de greffons personnalisés à partir des propres cellules du patient, éliminant ainsi les risques de rejet.
Modèles anatomiques précis pour planification chirurgicale
L'impression 3D permet de créer des modèles anatomiques précis basés sur les données d'imagerie médicale du patient. Ces modèles en trois dimensions aident les chirurgiens à mieux visualiser et comprendre l'anatomie spécifique du patient avant l'intervention. Cette approche est particulièrement utile pour les opérations complexes, comme les séparations de jumeaux siamois ou les reconstructions faciales.
Les modèles imprimés en 3D permettent aux chirurgiens de simuler l'intervention, d'anticiper les difficultés potentielles et de planifier la meilleure approche chirurgicale. Cela peut réduire considérablement le temps d'opération et améliorer les résultats pour le patient. De plus, ces modèles servent d'outils de communication précieux pour expliquer la procédure aux patients et à leurs familles, facilitant le consentement éclairé.
Dispositifs médicaux sur mesure par frittage laser sélectif
Le frittage laser sélectif (SLS) est une technique d'impression 3D particulièrement adaptée à la fabrication de dispositifs médicaux sur mesure. Cette technologie utilise un laser pour fusionner des particules de poudre, permettant de créer des objets complexes avec une grande précision. Elle est utilisée pour produire une variété de dispositifs médicaux, des orthèses aux instruments chirurgicaux personnalisés.
Un exemple notable est la fabrication d'attelles et de corsets orthopédiques. Traditionnellement, ces dispositifs étaient fabriqués manuellement, un processus long et imprécis. Avec l'impression 3D, il est possible de créer des orthèses parfaitement ajustées à la morphologie du patient, offrant un meilleur confort et une efficacité accrue. De plus, la liberté de conception offerte par l'impression 3D permet de créer des structures légères et aérées, améliorant la respirabilité et réduisant le poids du dispositif.
Aérospatiale et défense : impression 3D de pointe
L'industrie aérospatiale et de la défense est à l'avant-garde de l'adoption de l'impression 3D, exploitant cette technologie pour créer des composants légers, complexes et hautement performants. La capacité de l'impression 3D à produire des pièces avec des géométries impossibles à réaliser avec les méthodes traditionnelles ouvre de nouvelles possibilités en termes de design et de performance.
Pièces allégées pour avions par fusion sur lit de poudre
La fusion sur lit de poudre est une technique d'impression 3D métallique particulièrement adaptée à la fabrication de pièces aéronautiques. Elle permet de créer des structures internes complexes et des topologies optimisées, réduisant considérablement le poids des composants sans compromettre leur résistance. Cette réduction de poids se traduit directement par une diminution de la consommation de carburant et des émissions des avions.
Des constructeurs aéronautiques comme Airbus et Boeing utilisent déjà l'impression 3D pour produire des pièces critiques telles que des supports de moteur, des pales de turbine et des éléments de structure. Par exemple, le support de moteur imprimé en 3D d'Airbus pour l'A350 XWB est 30% plus léger que son équivalent fabriqué traditionnellement, tout en conservant les mêmes propriétés mécaniques. Cette innovation illustre parfaitement le potentiel de l'impression 3D pour révolutionner la conception aéronautique.
Prototypage rapide de composants satellites
Dans l'industrie spatiale, où chaque gramme compte, l'impression 3D offre des avantages considérables pour le prototypage et la fabrication de composants de satellites. La technologie permet de créer rapidement des prototypes fonctionnels, accélérant ainsi le processus de développement et réduisant les coûts. De plus, la possibilité de produire des pièces complexes en une seule opération simplifie l'assemblage et réduit le nombre de composants nécessaires.
Les antennes satellites sont un exemple parfait de l'utilisation de l'impression 3D dans ce domaine. Des structures d'antennes légères et complexes peuvent être imprimées en 3D, offrant des performances optimales tout en minimisant le poids. Cette approche permet également d'intégrer des canaux de refroidissement directement dans la structure de l'antenne, améliorant ainsi sa gestion thermique en orbite.
Fabrication additive de moteurs-fusées SpaceX
SpaceX a été un pionnier dans l'utilisation de l'impression 3D pour la fabrication de composants de moteurs-fusées. L'entreprise utilise cette technologie pour produire la chambre de combustion SuperDraco, un composant critique de son système d'abandon de lancement. L'impression 3D permet de créer cette pièce complexe en Inconel, un superalliage résistant aux hautes températures, en une seule opération.
Cette approche présente plusieurs avantages. Tout d'abord, elle réduit considérablement le temps de production, passant de plusieurs mois à quelques semaines. Ensuite, elle permet d'obtenir une pièce plus légère et plus résistante que son équivalent fabriqué traditionnellement. Enfin, la liberté de conception offerte par l'impression 3D permet d'optimiser la géométrie interne de la chambre de combustion, améliorant ainsi ses performances.
Équipements militaires personnalisés par dépôt de fil fondu
Dans le domaine de la défense, l'impression 3D par dépôt de fil fondu (FDM) est utilisée pour créer rapidement des équipements personnalisés et des pièces de rechange sur le terrain. Cette technologie relativement simple et robuste est particulièrement adaptée aux environnements difficiles dans lesquels opèrent les forces armées.
Par exemple, l'armée américaine expérimente l'utilisation d'imprimantes 3D pour produire des pièces de rechange pour les véhicules et l'équipement directement sur les théâtres d'opérations. Cela permet de réduire considérablement les délais d'approvisionnement et les coûts logistiques associés au transport de pièces détachées. De plus, la possibilité de personnaliser l'équipement en fonction des besoins spécifiques des soldats ou des missions améliore l'efficacité opérationnelle.
Automobile : production efficiente par fabrication additive
L'industrie automobile adopte de plus en plus l'impression 3D pour optimiser ses processus de conception et de fabrication. Cette technologie offre des avantages significatifs en termes de rapidité, de flexibilité et de personnalisation, permettant aux constructeurs de répondre plus efficacement aux demandes du marché et aux exigences réglementaires.
Outillage et moules d'injection imprimés en 3D
L'un des domaines où l'impression 3D a un impact majeur dans l'industrie automobile est la fabrication d'outils et de moules. Traditionnellement, la production de moules d'injection pour les pièces en plastique était un processus long et coûteux. Avec l'impression 3D, il est désormais possible de créer des moules et des inserts de moule en quelques jours plutôt qu'en plusieurs semaines.
Cette rapidité permet aux constructeurs automobiles de réaliser des itérations de conception plus rapides et de tester différentes versions de pièces avant de s'engager dans la production en série. De plus, l'impression 3D permet de créer des canaux de refroidissement conformes dans les moules, optimisant ainsi le processus d'injection et réduisant les temps de cycle. Cette approche améliore non seulement la qualité des pièces produites, mais augmente également la productivité globale.
Pièces de rechange à la demande pour véhicules classiques
L'impression 3D offre une solution élégante au problème de disponibilité des pièces de rechange pour les véhicules classiques ou anciens. Souvent, les pièces d'origine ne sont plus fabriquées, rendant la restauration et l'entretien de ces véhicules difficiles et coûteux. Grâce à l'impression 3D, il est possible de reproduire ces pièces à la demande, même en petites quantités.
Porsche Classic, par exemple, utilise l'impression 3D pour produire des pièces de rechange rares pour ses modèles anciens. Cette approche permet non seulement de maintenir ces véhicules de collection en état de marche, mais offre également une solution plus durable en évitant la surproduction et le stockage à long terme de pièces peu demandées. De plus, l'impression 3D permet d'améliorer certaines pièces en utilisant des matériaux modernes plus performants, tout en conservant l'aspect et la fonctionnalité d'origine.
Prototypes fonctionnels par stéréolithographie
La stéréolithographie (SLA) est une technique d'impression 3D particulièrement appréciée dans l'industrie automobile pour la création de prototypes fonctionnels. Cette technologie offre une excellente précision et une finition de surface lisse, idéale pour créer des maquettes de design intérieur et extérieur, ainsi que des prototypes de pièces mécaniques.
Les constructeurs automobiles utilisent la SLA pour créer rapidement des modèles de tableaux de bord, de consoles centrales et d'autres éléments intérieurs. Ces prototypes permettent aux designers et aux ingénieurs d'évaluer l'ergonomie, l'esthétique et la fonctionnalité des composants avant la production en série. La SLA est également utilisée pour créer des prototypes de phares et de feux arrière, permettant de
tester les propriétés optiques des composants, un élément crucial dans le développement de systèmes d'éclairage innovants et économes en énergie.
Architecture et construction : impression 3D à grande échelle
L'industrie de la construction adopte progressivement l'impression 3D pour révolutionner la façon dont nous concevons et construisons nos bâtiments. Cette technologie offre des possibilités fascinantes en termes de liberté de conception, de rapidité d'exécution et de durabilité.
Maisons imprimées en béton par COBOD BOD2
L'une des applications les plus spectaculaires de l'impression 3D dans la construction est la réalisation de maisons entières. La société danoise COBOD a développé l'imprimante BOD2, capable d'imprimer des structures en béton à grande échelle. Cette technologie permet de construire les murs d'une maison en quelques jours seulement, réduisant considérablement le temps et les coûts de construction.
Le processus consiste à extruder un mélange de béton spécialement conçu couche par couche, suivant un modèle 3D prédéfini. Cette approche offre une grande flexibilité dans la conception architecturale, permettant de créer des formes courbes et complexes difficiles à réaliser avec les méthodes de construction traditionnelles. De plus, l'impression 3D réduit les déchets de construction et la main-d'œuvre nécessaire, rendant le processus plus durable et économique.
Structures complexes par extrusion de matériaux composites
Au-delà du béton, l'impression 3D en architecture explore l'utilisation de matériaux composites pour créer des structures légères et résistantes. Des entreprises comme Branch Technology utilisent des robots pour extruder des filaments de polymère renforcé de fibres, créant ainsi des structures en treillis complexes qui peuvent ensuite être remplies de matériaux isolants ou structurels.
Cette technique permet de réaliser des formes organiques et des géométries complexes impossibles à obtenir avec les méthodes de construction conventionnelles. Elle ouvre la voie à une nouvelle esthétique architecturale, tout en offrant des avantages en termes de performance structurelle et d'efficacité énergétique. Par exemple, ces structures en treillis peuvent intégrer des systèmes de ventilation naturelle ou servir de support pour des façades végétalisées, contribuant ainsi à la création de bâtiments plus écologiques et durables.
Restauration patrimoniale par numérisation et réplication 3D
L'impression 3D joue également un rôle crucial dans la préservation et la restauration du patrimoine architectural. Grâce aux techniques de numérisation 3D, il est possible de créer des répliques exactes d'éléments architecturaux historiques endommagés ou disparus. Cette approche est particulièrement précieuse pour la restauration de bâtiments classés ou de monuments historiques.
Par exemple, après l'incendie de la cathédrale Notre-Dame de Paris en 2019, des équipes ont utilisé des scans 3D préexistants pour créer des modèles numériques précis de la structure. Ces données pourront être utilisées pour imprimer en 3D des éléments de remplacement, assurant une fidélité maximale à l'original. Cette technologie permet non seulement de préserver notre patrimoine architectural, mais aussi de le rendre plus accessible grâce à la création de répliques pour les musées ou les expositions.
Industrie de la mode : personnalisation par fabrication additive
L'industrie de la mode embrasse l'impression 3D pour offrir des produits personnalisés et innovants, repoussant les limites de la créativité et de la fonctionnalité dans le domaine de l'habillement et des accessoires.
Bijoux sur mesure par fusion laser sélective
La fusion laser sélective (SLM) révolutionne la création de bijoux en permettant la fabrication de pièces complexes et uniques impossibles à réaliser avec les techniques traditionnelles. Cette technologie offre aux designers une liberté créative sans précédent, leur permettant de concevoir des structures intriquées et des formes organiques qui défient les limites de la joaillerie classique.
Des marques comme Ica & Kostika utilisent l'impression 3D pour créer des collections de bijoux avant-gardistes, combinant des designs complexes avec des matériaux précieux comme l'or et l'argent. Cette approche permet non seulement de réduire les délais de production et les coûts, mais aussi d'offrir aux clients des pièces véritablement uniques et personnalisées.
Chaussures adaptatives imprimées par adidas futurecraft
Adidas a fait sensation dans l'industrie de la chaussure avec sa ligne Futurecraft, qui utilise l'impression 3D pour créer des semelles intermédiaires sur mesure. Cette technologie permet de produire des chaussures parfaitement adaptées à la morphologie du pied et à la démarche de chaque utilisateur, offrant un niveau de confort et de performance inégalé.
Le processus implique la numérisation du pied du client et l'analyse de sa démarche pour créer un modèle 3D personnalisé. La semelle intermédiaire est ensuite imprimée en 3D avec un matériau élastomère qui offre des propriétés d'amorti et de rebond optimales. Cette approche ouvre la voie à une nouvelle ère de chaussures de sport hautement personnalisées, où chaque paire est conçue pour répondre aux besoins spécifiques de son utilisateur.
Textiles techniques par impression 3D de filaments flexibles
L'impression 3D de filaments flexibles permet de créer des textiles techniques aux propriétés uniques. Cette technologie est utilisée pour produire des vêtements et accessoires innovants qui combinent fonctionnalité et esthétique futuriste. Par exemple, la designer Danit Peleg a créé une collection de mode entièrement imprimée en 3D, utilisant des filaments flexibles pour créer des tissus légers et respirants.
Cette approche offre de nombreux avantages, notamment la possibilité de créer des structures textiles complexes impossibles à tisser ou à tricoter traditionnellement. Elle permet également d'intégrer directement des fonctionnalités dans le tissu, comme des zones de ventilation ou de compression. De plus, l'impression 3D de vêtements ouvre la voie à une production à la demande, réduisant ainsi les déchets et l'inventaire excédentaire si courants dans l'industrie de la mode.