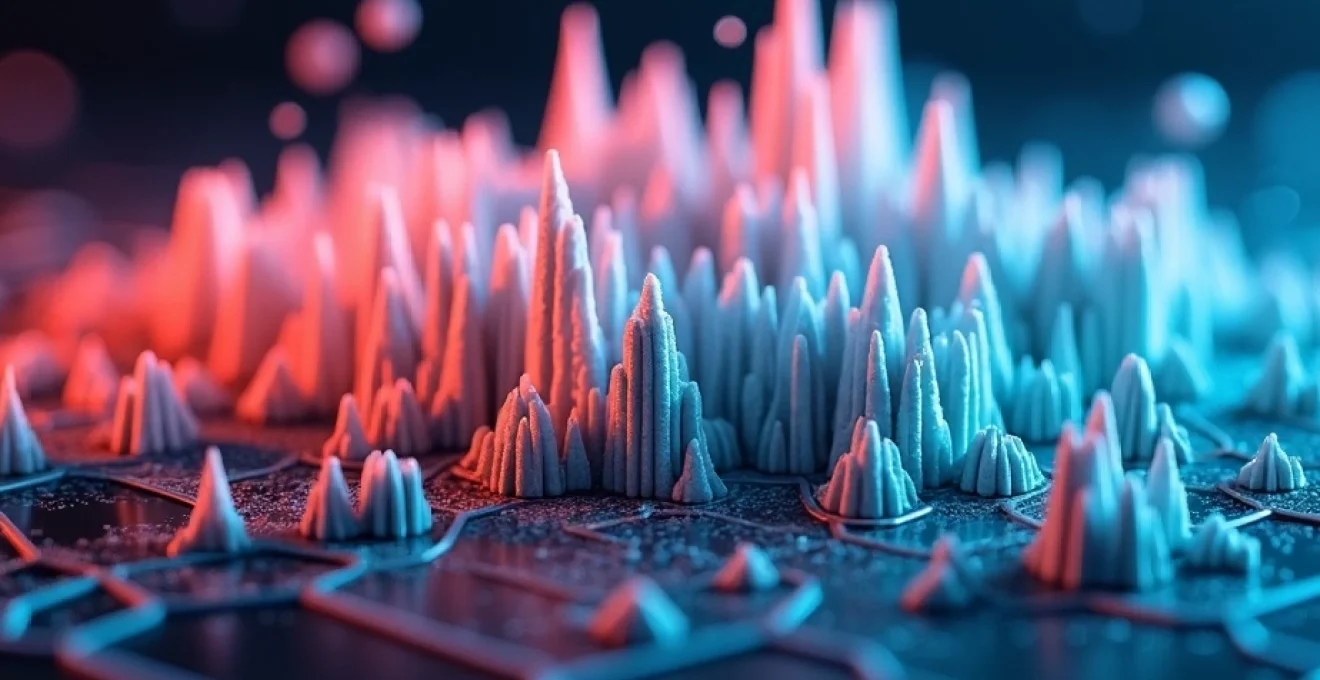
L'impression 3D révolutionne le processus de prototypage dans de nombreux secteurs industriels. Cette technologie permet de créer rapidement et avec précision des modèles physiques à partir de concepts numériques. Grâce à sa flexibilité et sa rapidité, l'impression 3D offre aux ingénieurs et designers la possibilité d'itérer plus efficacement leurs designs, réduisant ainsi les délais et coûts de développement. De la validation de concept aux tests fonctionnels, en passant par l'optimisation topologique, l'impression 3D s'impose comme un outil incontournable du prototypage moderne. Explorons en détail comment cette technologie transforme le cycle de développement produit et permet aux entreprises d'innover plus rapidement.
Technologies d'impression 3D pour le prototypage rapide
Plusieurs technologies d'impression 3D se démarquent pour le prototypage rapide, chacune avec ses avantages spécifiques. La stéréolithographie (SLA) offre une excellente précision et un état de surface lisse, idéal pour les prototypes esthétiques ou nécessitant des détails fins. Le dépôt de fil fondu (FDM) se distingue par sa simplicité d'utilisation et son faible coût, le rendant accessible pour de nombreuses applications. Le frittage sélectif par laser (SLS) permet quant à lui de créer des pièces fonctionnelles robustes sans supports.
Le choix de la technologie dépend des exigences du prototype en termes de précision, de propriétés mécaniques et de délais. Par exemple, pour un prototype visuel d'un boîtier électronique, la SLA sera privilégiée pour son rendu lisse. En revanche, pour tester l'assemblage mécanique d'un produit, le FDM ou le SLS seront plus adaptés grâce à leur résistance accrue.
L'impression 3D multi-matériaux gagne également en popularité pour le prototypage. Elle permet de combiner différentes propriétés au sein d'une même pièce, comme la rigidité et la flexibilité. Cette polyvalence ouvre de nouvelles possibilités en termes de design et de fonctionnalités pour les prototypes.
Matériaux avancés pour l'impression 3D de prototypes
L'évolution des matériaux d'impression 3D a considérablement élargi le champ des possibles pour le prototypage. Au-delà des plastiques standards comme l'ABS ou le PLA, de nouveaux matériaux aux propriétés avancées sont désormais disponibles. Les résines techniques, par exemple, offrent des caractéristiques proches des thermoplastiques d'ingénierie, permettant la création de prototypes fonctionnels plus représentatifs.
Les matériaux composites, incorporant des fibres de carbone ou de verre, apportent une résistance accrue tout en conservant la légèreté. Ils sont particulièrement appréciés dans l'industrie automobile ou aérospatiale pour tester des pièces soumises à des contraintes élevées. Les élastomères imprimables en 3D permettent quant à eux de prototyper des pièces flexibles comme des joints ou des amortisseurs.
L'impression 3D métallique, bien que plus coûteuse, trouve sa place dans le prototypage de pièces hautement techniques. Elle permet de créer des prototypes en acier, titane ou aluminium, offrant des propriétés mécaniques et thermiques proches des pièces finales. Cette technologie est particulièrement utile pour valider la conception de pièces destinées à être produites par fabrication additive métallique.
L'utilisation de matériaux biocompatibles ouvre également de nouvelles perspectives dans le domaine médical, permettant le prototypage rapide d'implants ou de prothèses personnalisées.
Le choix du matériau est crucial pour obtenir un prototype représentatif. Il faut considérer non seulement les propriétés mécaniques, mais aussi la stabilité dimensionnelle, la résistance chimique ou encore la biocompatibilité selon l'application visée. L'expertise dans la sélection et l'utilisation de ces matériaux avancés devient un atout majeur pour optimiser le processus de prototypage.
Optimisation des paramètres d'impression pour la qualité des prototypes
La qualité d'un prototype imprimé en 3D dépend grandement de l'optimisation des paramètres d'impression. Ces réglages influencent non seulement l'aspect visuel de la pièce, mais aussi ses propriétés mécaniques et sa précision dimensionnelle. Une compréhension approfondie de ces paramètres est essentielle pour tirer le meilleur parti de l'impression 3D dans le processus de prototypage.
Résolution et épaisseur de couche pour la précision dimensionnelle
La résolution d'impression, souvent exprimée en microns, détermine la finesse des détails que vous pouvez obtenir sur votre prototype. Une résolution plus élevée permet de reproduire des géométries complexes avec précision, mais augmente également le temps d'impression. L'épaisseur de couche, quant à elle, affecte directement la précision verticale et l'apparence de la surface. Des couches plus fines donnent un meilleur état de surface mais rallongent le temps d'impression.
Pour optimiser ces paramètres, il faut trouver un équilibre entre la précision requise et le temps de fabrication acceptable. Par exemple, pour un prototype fonctionnel où la précision dimensionnelle est cruciale, comme une pièce d'engrenage, vous opterez pour une résolution élevée et des couches fines. En revanche, pour un prototype conceptuel rapide, des couches plus épaisses peuvent suffire.
Vitesse d'impression et refroidissement pour la stabilité structurelle
La vitesse d'impression influe directement sur la qualité et la résistance de la pièce imprimée. Une vitesse trop élevée peut entraîner des défauts comme des décalages entre les couches ou des déformations, particulièrement visibles sur les surfaces inclinées. À l'inverse, une vitesse trop lente augmente inutilement le temps de fabrication.
Le refroidissement joue un rôle crucial, notamment pour les pièces en surplomb ou les petits détails. Un refroidissement efficace permet une solidification rapide du matériau déposé, améliorant ainsi la précision géométrique et réduisant les risques de déformation. Pour des matériaux techniques comme le nylon ou l'ABS, un contrôle précis du refroidissement est essentiel pour éviter le gauchissement et assurer la stabilité dimensionnelle du prototype.
Densité de remplissage et motifs pour les propriétés mécaniques
La densité de remplissage et le motif utilisé influencent directement les propriétés mécaniques du prototype. Une densité plus élevée augmente la résistance et la rigidité de la pièce, mais aussi son poids et le temps d'impression. Les motifs de remplissage, tels que le nid d'abeille ou le gyroïde, offrent différents compromis entre résistance et légèreté.
Pour un prototype fonctionnel devant subir des contraintes mécaniques, comme une pièce de fixation, une densité de remplissage élevée (60-100%) avec un motif robuste sera préférable. En revanche, pour un prototype purement visuel, une faible densité (10-20%) suffira, réduisant ainsi le temps et le coût d'impression.
Orientation et supports pour la fidélité géométrique
L'orientation de la pièce sur le plateau d'impression est un facteur souvent sous-estimé mais crucial pour la qualité du prototype. Elle influence non seulement la résistance de la pièce selon les directions de sollicitation, mais aussi la quantité de supports nécessaires et la qualité de surface obtenue.
Les supports, bien que parfois inévitables, peuvent laisser des marques sur la surface du prototype. Une orientation judicieuse permet de minimiser leur utilisation et de les placer sur des zones non critiques. Pour des pièces complexes, des logiciels d'optimisation d'orientation peuvent vous aider à trouver le meilleur compromis entre qualité de surface, précision dimensionnelle et temps d'impression.
L'optimisation des paramètres d'impression est un art qui requiert expérience et expérimentation. Chaque prototype peut nécessiter une approche différente pour atteindre le meilleur résultat possible.
Post-traitement des prototypes imprimés en 3D
Le post-traitement est une étape cruciale pour améliorer la qualité finale des prototypes imprimés en 3D. Il permet non seulement d'affiner l'aspect esthétique mais aussi d'améliorer les propriétés mécaniques et fonctionnelles des pièces. Les méthodes de post-traitement varient selon la technologie d'impression utilisée et les exigences du prototype.
Pour les pièces imprimées par FDM, le ponçage est souvent la première étape pour lisser les lignes de couche visibles. Il peut être suivi d'un traitement chimique, comme l'exposition à des vapeurs d'acétone pour l'ABS, qui permet de fondre légèrement la surface et d'obtenir un fini plus lisse. Pour les pièces SLA, le nettoyage à l'alcool isopropylique et la post-polymérisation UV sont essentiels pour assurer la résistance et la stabilité de la résine.
Les techniques de finition comme la peinture, le plaquage métallique ou l'application de revêtements spéciaux permettent d'améliorer l'apparence et les propriétés de surface des prototypes. Ces traitements peuvent simuler l'aspect de différents matériaux ou ajouter des fonctionnalités comme la résistance à l'abrasion ou aux UV.
Pour les prototypes fonctionnels, des traitements thermiques peuvent être appliqués pour améliorer les propriétés mécaniques. Par exemple, le recuit des pièces imprimées en nylon peut augmenter significativement leur résistance et leur stabilité dimensionnelle. L'infiltration de résine est une autre technique permettant de renforcer les pièces imprimées en poudre (SLS) et d'améliorer leur étanchéité.
Il est important de noter que le post-traitement peut affecter les dimensions finales du prototype. Une compensation peut être nécessaire lors de la conception pour prendre en compte ces variations. L'expertise dans les techniques de post-traitement devient donc un atout majeur pour produire des prototypes de haute qualité répondant précisément aux exigences du projet.
Intégration de l'impression 3D dans le cycle de développement produit
L'intégration de l'impression 3D dans le cycle de développement produit transforme radicalement la manière dont les entreprises conçoivent, testent et itèrent leurs produits. Cette technologie s'insère à différentes étapes du processus, de la conception initiale à la pré-production, offrant une flexibilité et une rapidité sans précédent.
Conception assistée par ordinateur (CAO) pour l'impression 3D
La conception pour l'impression 3D ( Design for Additive Manufacturing ou DfAM) est devenue une compétence essentielle pour les ingénieurs et designers. Elle implique de repenser les approches traditionnelles de conception pour tirer pleinement parti des possibilités offertes par la fabrication additive. Les logiciels de CAO modernes intègrent désormais des outils spécifiques pour optimiser les designs en vue de l'impression 3D.
L'optimisation topologique, par exemple, permet de créer des structures allégées tout en conservant les propriétés mécaniques nécessaires. Cette approche est particulièrement valorisée dans les industries aérospatiale et automobile, où la réduction de poids est cruciale. Les designers peuvent également explorer des géométries complexes, impossibles à réaliser avec les méthodes de fabrication traditionnelles, ouvrant ainsi de nouvelles possibilités d'innovation.
Itérations rapides et validation de concept avec prototypes imprimés
L'un des principaux avantages de l'impression 3D dans le cycle de développement est la possibilité de réaliser des itérations rapides. Les concepteurs peuvent passer du modèle numérique au prototype physique en quelques heures, permettant une évaluation immédiate du design. Cette rapidité facilite la détection précoce des problèmes et encourage l'exploration de multiples variations de conception.
La validation de concept devient plus tangible avec des prototypes physiques. Les équipes de développement, les clients et les parties prenantes peuvent interagir directement avec le produit, ce qui améliore la communication et accélère la prise de décision. Cette approche hands-on est particulièrement précieuse pour évaluer l'ergonomie, l'esthétique et l'utilisabilité des produits.
Tests fonctionnels sur prototypes imprimés en 3D
Au-delà des prototypes purement visuels, l'impression 3D permet de créer des prototypes fonctionnels pour des tests approfondis. Grâce aux matériaux avancés et aux techniques d'impression de haute précision, il est possible de produire des pièces aux propriétés proches de celles du produit final.
Ces prototypes peuvent être soumis à des tests de résistance, d'assemblage, de flux, ou même de performance dans des conditions réelles d'utilisation. Par exemple, dans l'industrie automobile, des pièces de carrosserie imprimées en 3D peuvent être testées en soufflerie pour évaluer leur aérodynamisme. Dans le secteur médical, des prothèses personnalisées peuvent être essayées et ajustées avant la production finale.
Transition du prototype imprimé 3D vers la production en série
La transition du prototype à la production en série reste un défi, mais l'impression 3D joue un rôle croissant dans ce processus. Pour les petites séries ou les produits personnalisés, l'impression 3D peut même être utilisée comme méthode de production finale, éliminant le besoin de passer à des techniques de fabrication traditionnelles.
Pour les productions à plus grande échelle, les prototypes imprimés en 3D servent de référence pour la conception des moules d'injection ou des outillages. Ils permettent de valider les designs avant d'investir dans des outils de production coûteux. De plus, l'impression 3D est de plus en plus utilisée pour créer des outils de production, comme des gabarits, des fixations ou des moules rapides, accélérant ainsi le passage à la production.
L'intégration de l'impression 3D dans le cycle de développement produit ne se limite pas à la création de prototypes. Elle influence l'ensemble du processus, de la conception initiale à la production, en passant par les tests et la validation. Cette approche holistique permet aux entreprises d'
innover plus rapidement et de réduire significativement les délais de mise sur le marché de nouveaux produits.
Cas d'utilisation de l'impression 3D pour le prototypage industriel
L'impression 3D s'est imposée comme un outil incontournable dans de nombreux secteurs industriels pour le prototypage. Son utilisation permet non seulement d'accélérer le processus de développement, mais aussi d'explorer des designs innovants et d'optimiser les produits avant leur production à grande échelle.
Dans l'industrie automobile, les constructeurs utilisent l'impression 3D pour créer rapidement des maquettes de design intérieur et extérieur. Ces prototypes permettent d'évaluer l'ergonomie, l'esthétique et l'aérodynamisme des véhicules avant la production des outils de fabrication coûteux. Par exemple, BMW utilise des prototypes imprimés en 3D pour tester l'assemblage de composants complexes et optimiser les processus de production.
Le secteur aérospatial bénéficie grandement de l'impression 3D pour le prototypage de pièces légères et complexes. Airbus, par exemple, utilise cette technologie pour créer des prototypes de supports de câblage et de conduits d'air optimisés topologiquement. Ces pièces, une fois validées, peuvent être directement produites en série par fabrication additive, réduisant ainsi le poids des avions et leur consommation de carburant.
Dans l'industrie médicale, l'impression 3D révolutionne la création de prothèses et d'implants personnalisés. Les chirurgiens peuvent désormais imprimer des modèles anatomiques spécifiques aux patients pour planifier des interventions complexes. Ces prototypes permettent non seulement d'améliorer la précision des opérations, mais aussi de réduire les temps d'intervention et les risques pour les patients.
L'impression 3D dans le secteur médical ne se limite pas aux prothèses ; elle s'étend à la création de modèles d'organes pour la formation des médecins et à la conception de dispositifs médicaux sur mesure.
Le secteur de l'électronique grand public utilise l'impression 3D pour prototyper rapidement les boîtiers et les composants de nouveaux appareils. Cette approche permet aux concepteurs de tester différentes configurations ergonomiques et esthétiques avant de s'engager dans la production de masse. Des entreprises comme Apple et Samsung utilisent cette technologie pour garder une longueur d'avance dans un marché en constante évolution.
Dans l'industrie du jouet, l'impression 3D accélère considérablement le processus de développement de nouveaux produits. Les fabricants peuvent créer des prototypes fonctionnels de figurines, de jeux de construction ou de jouets éducatifs en quelques jours, permettant des tests utilisateurs précoces et des ajustements rapides basés sur les retours.
L'industrie de la mode et des accessoires exploite également le potentiel de l'impression 3D pour le prototypage. Des marques de chaussures comme Adidas et New Balance utilisent cette technologie pour concevoir et tester de nouvelles semelles avec des structures complexes impossibles à réaliser avec les méthodes traditionnelles. Dans la bijouterie, l'impression 3D permet de créer des prototypes de pièces uniques ou de collections entières, permettant aux designers d'explorer des formes audacieuses avant la production en métaux précieux.
Le secteur de l'outillage industriel bénéficie aussi de l'impression 3D pour le prototypage rapide. Les fabricants peuvent créer des prototypes fonctionnels d'outils, de moules et de gabarits pour tester leur efficacité avant la production finale. Cette approche permet non seulement d'optimiser la conception des outils, mais aussi de réduire les coûts et les délais de développement.
Enfin, dans le domaine de l'architecture et de la construction, l'impression 3D est utilisée pour créer des maquettes détaillées de bâtiments et d'infrastructures. Ces prototypes permettent aux architectes et aux ingénieurs de visualiser les projets en trois dimensions, d'évaluer différentes options de design et de communiquer efficacement avec les clients et les parties prenantes.
L'adoption croissante de l'impression 3D pour le prototypage industriel témoigne de sa capacité à accélérer l'innovation, réduire les coûts de développement et améliorer la qualité des produits finaux. À mesure que la technologie continue d'évoluer, on peut s'attendre à voir son utilisation s'étendre à de nouveaux secteurs et applications, renforçant ainsi son rôle crucial dans le processus de développement de produits.